A First Look at Joby’s eVTOL Future
The production model is ready for flight test, but are we ready to fly?
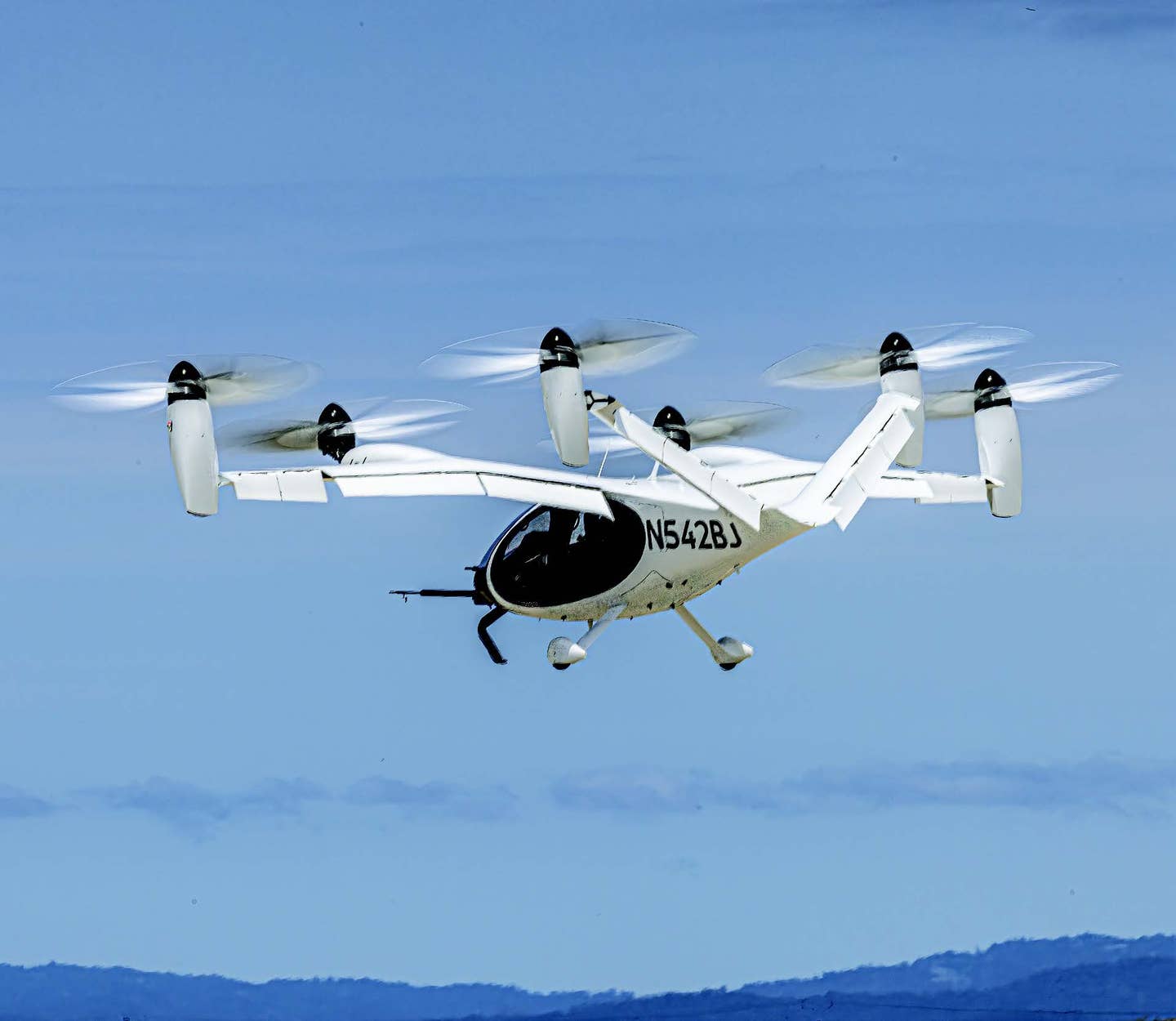
We observed Joby flight in the sim in D.C., at left, and watching the remotely piloted demo flight at Marina, above. [Stephen Yeates]
Joby Aviation glows with the shining health of an organization led by a vision drawn from childhood dreams. The California-born-and-bred company, founded by JoeBen Bevirt, feels clear in its purpose: to make the most challenging “last mile” of aerial transport between points an accessible—and quiet—reality.
Bevirt thought up the premise for an electric vertical takeoff and landing aircraft (eVTOL) as he walked home from the last point a school bus could take him near his home in California’s Santa Cruz Mountains. Today, Joby is a roughly $4 billion-cap enterprise on the cusp of its type certification for-credit testing with the FAA on an evolution of the very vehicle Bevirt envisioned would lift him from that dusty bus stop into the peaceful meadow near his parents’ forest home.
If you're not already a subscriber, what are you waiting for? Subscribe today to get the issue as soon as it is released in either Print or Digital formats.
Subscribe NowFrom a flying prototype launched in an empty quarry in 2010 to the first flight of the latest conforming production prototype, the final iteration of this initial commercially viable eVTOL will carry a pilot and up to four passengers as far as a 100 sm range solely using electric motors, bringing with it a new way of managing flight.
However, though the Joby aircraft is piloted, the team is not building an aircraft for pilots. By deliberate choice, the idiosyncrasies that make up the kinesthetic joy of flying are dialed out of the aircraft’s flight control system—they have to be in order to make the Joby fly like it does. You can hand fly it, sure, but like other aircraft aimed at owner operators who are new to the game and not interested in the romance of flight, you’re in a version of autoflight all the time. In fact, an autopilot per se is unnecessary because the foundations of autoflight run continuously—designed to manage the cascade of failures and corners of the envelope we train so hard to avoid and mitigate and respond to.
- READ MORE: We Fly: Diamond DA62
While we can’t yet fly the version slated for the final rounds of type certificate (TC) testing—the production aircraft, in company parlance—we can fly the sim. As one six-month Joby employee at the company’s Washington, D.C., office told me, even they like to fly it—and they’re not into driving themselves anywhere. Being “in control” just doesn’t interest them—quite a change from what we think of as a pilot.
So where is this going? I had to find out for myself. In a series of introductions, I visited Joby’s R&D and production facilities in Santa Clara and Marina, California, last summer and Joby’s offices in D.C. in January, along with an interview with Bevirt at the Paris Air Show in June, which we covered in Issue 940 (“In Depth”).
How It Works
The Joby aircraft consists of a rounded, wide-windowed fuselage to carry passengers with a single pilot seat up front. A wing transects the top at about its midsection, with a V-shaped tail in the back. Six equally sized rotors stand in a roughly hexagonic position: two in front, two at the wingtips, and two aft, on the apex of each V in the tail. They pivot and rotate in such a way as to produce both thrust translating into airspeed and thrust directed for flight control. The aircraft also uses ailerons and ruddervators (akin to those on the Vision Jet or V35 Bonanza). But those are sectioned, with two sets of aileron-style controls on the wings and three sections of ruddervators on the V-shaped tail.
The previous conforming prototype version had flaps, but according to Greg Bowles, head of government affairs for Joby, “they didn’t buy their way onto the production version.” In other words, no need for them. The six motors obtain their juice from a series of battery packs, but these are unlike any created for electric aircraft thus far. They work in pairs for each motor and in isolation from the other pairs so that they are doubly redundant. We learned how Joby arrived at this arrangement—along with other details regarding their makeup—when we walked through the plant at Santa Clara earlier on the day of our visit preparing us for the observation of the remotely piloted demo flight of the preproduction prototype later on.
With an aspect that looks like a helicopter with six rotors instead of main and tail rotors, the quietness of the Joby’s departure struck me immediately. Normally, hearing the main rotor spool up causes you to plug your ears against the sound. But with the powering up and lifting off of the Joby, the high-pitched rpm of the blades barely registered over the wind about 100 feet away.
A New Kind of Motor
The “engine” driving the Joby aircraft is unlike any motor I’ve ever seen. Granted, I’m not versed in much outside of the two- and four-stroke combustion engines that provide thrust for light airplanes and the odd motorbike. But this is essentially a 3D-printed titanium ring. A doughnut of sorts, outlined by a series of copper-and- tan-colored power packs.
A lot of people have asked why Joby didn’t buy motors from another company—with so many electric choices out there on the market. “What we found was that [by] making it fit exactly for purpose, we could do much better in terms of weight and size,” said Jon Wagner—head of batteries, powertrain, and electronics and based at the Santa Clara facility—during our tour. The core starts with a 3D-printed titanium housing in the middle, and the magnetics that drive the rotation are made from copper and steel. “And we buy big rolls of copper and big sheets of steel, and we build this thing up out of the raw materials,” said Wagner. At the D.C. office, Bowles handed me a featherweight bottle opener made from the remnant titanium dust—an elegant example of upcycling waste from the process.
Three pins, and three pins—this is actually two motors, with two sets of three-phase windings. “That’s two different electrical circuits inside this motor that drive the rotation,” said Wagner. “So if you have a failure, you’ve segmented the system and now you have a secondary means of driving the motor.” The electronic brain that’s always on in the background figures out how to redistribute the remaining power, cycling up and down as needed for both thrust and flight control. This requires a new way of managing that control.
Unified in Flight
The world of eVTOL will almost certainly be based on the use of “simplified flight controls”—as outlined in the Modernization of Special Airworthiness Certificates (MOSAIC), which update light sport aircraft (LSA) certification but also set the stage for use of similar regulatory structure in the Special Federal Aviation Regulations (SFARs) covering eVTOLs.
The simplified flight control is simple to the pilot— taking the most basic of inputs and figuring out what the pilot wants to have happen and ensconcing them in a swaddle of envelope protection so they will neither stall nor exceed limit load factors. To do this, those controls are anything but simple under the surface. Joby has patterned these after the unified controls in high-end military hardware, such as the F-35.
The Joby aircraft is flown with a power lever in the left hand and a joystick-style flight control in the right—and you sit in a single seat centered in the cockpit. Though at first it feels familiar, you don’t use the control stick in quite the same way as you do in a traditional airplane—you rarely hold in continuous pressure, for example. So it’s OK that it’s purposefully stiff. You give input, then take it out. The power lever is similarly centering—hold in to speed up in airplane mode, and leave it in place while in TRC (translate, or hover) mode. You twist to yaw about the vertical axis in translate mode, and you bank to either translate or side step while in TRC or bank while flying the wing. But you don’t need to hold back pressure in the bank to maintain a level attitude since the rotors are compensating for the change in lift vector direction.
To illustrate, let’s look at one common failure mode in rotorcraft: One commonality to the Joby is the bearing plate—“but we can get around it,” said Bowles. If there’s a motor failure, the computer picks up load, slows the rotor on the diagonal corner, and speeds up the rest. The aircraft also retains the ability to glide on its wing—so Joby has tested that mode as well—which, as a fixed-wing pilot, I admit helps me wrap my brain around the whole package.
On Speed, On Target
You don’t think of stall speeds and VNE in the same way either, since the aircraft’s flight computers protect you from those exceedances in most all situations. “It is important to understand that the aircraft has 6 propellers and 10 control surfaces along with a rather advanced fly-by-wire control system,” said Jason Thomas, flight engineering lead for Joby, “and those propellers can tilt as well as change their blade pitch...It creates a situation, unlike a traditional fixed wing aircraft or helicopter, where there is more than one way to trim the aircraft at a given state or maneuver.”
How will pilots transition to Joby? It helps that the controls feel fairly intuitive. In my sim flights at Marina and D.C., it took just a few minutes to understand how to take off, land, and maneuver in the traffic pattern at a normal airport—KOAR and KSEA were programmed into the sim—during a standard flight. The FAA has established an SFAR for existing pilots under the powered-lift category—and the goal is to allow them to transition by taking essentially a type-rating course.
As a foundation for its business model, Joby established a Part 135 operation using a Cirrus SR22 between KSQL, Palo Alto, California, and KOAR. It plans to add the SFAR-covered aircraft to the certificate, with a track record in flight operations, maintenance, and safety management with the local FSDO. Similarly, the company has also set up a Part 141 operation, training internal pilots, to which it will add the Joby aircraft.
And the proof, then, will be flying the actual aircraft—and seeing just how that feels as a pilot.
Cockpit at a Glance
A. The pair of displays can be laid out in many ways for the pilot. The MFD hosts the power and propulsion system schematic in this view.
B. The primary flight display features a familiar Garmin interface, with airspeed and altitude tapes, plus standardized callouts for winged and vertical flight regime modes.
C. A Garmin GTC-style touchscreen controller also feels familiar to many pilots, following on to the similar control unit found in many new piston and turboprop airplanes and rotorcraft.
D. The power lever on the left side of the pilot’s seat is self-centering and allows for acceleration and deceleration control, as opposed to placing it at a given power setting.
E. The flight control stick self centers as well as twists for yaw control and banks to either turn or translate sideways, depending on the flight mode.
Spec Sheet: Joby Aircraft
Price, Projected: Not for sale, operated exclusively by Joby
Propulsion System: 6 electric dual wound motors, 4 on the wings, 2 on the V-tail
Crew: 1
Passenger Seats: 4
Length: 21 ft.
Height: TK
Wingspan: 39 ft.
Maximum Takeoff Weight: 5,300 lbs.
Empty Weight: TK
Useful Load/Payload: 1,000 lbs.
Cabin Width: TK
Cabin Height: TK
Power Capacity: Four lithium-ion battery packs
Endurance: TK
Range: Up to 100 sm (87 nm)
Liftoff Speed: Hover
Top Speed: 170 kt (200 mph)
Landing Speed: Hover
Stall Speed: N/A
Part Two: Building the Childhood Dream
It starts with a specific type of composite.
The sourcing of the raw materials to make the part that goes into the component that tucks into an aircraft in a strategic place—in the post-pandemic global aerospace industry, that perhaps is not so uncommon.
But when Joby Aviation first began coalescing into reality in various warehouses in the Bay Area southeast of San Francisco, most manufacturers didn’t get involved with the creation of the material—let alone purchasing the raw stuff from which to produce minor hardware in house.
That’s exactly what Joby has been up to since those early days—the development of the requirement alongside the technology needed to deliver the performance and capability of a new type of aircraft. By taking control of every aspect of the requirement to the final disposition of a part, it gets more precisely what it wants.
Diving into the Works
We took a walk around the skunk works—well, just one portion of them—in nondescript buildings, feeling like we were walking through a back lot on land adjacent to the San Carlos Regional Airport (KSQL). Leading the way was the perfect guide, Jon Wagner, as noted, Joby’s head of batteries, powertrain, and electronics. If that job title feels a bit cobbled together, it’s not. He’s the juice guy—how to store it and how to deliver it to the motors as well as the avionics and flight control system.
Working with Wagner is Jason Thomas, flight engineering lead. Thomas came to the company in 2021 from a designated engineering representative firm in Florida called EQ Dynamics. Before that, he worked with Aurora Flight Systems and its UAS concepts, and prior to that, at Honda Aircraft Company and Gulfstream Aerospace, in flutter and structural engineering roles. “I am the sole DER for external loads, aeroelasticity (flutter), and ground vibration testing (GVT),” said Thomas of the fascinating confluence of disciplines that by necessity must cover new territory in just about every mode of flight on the airframe.
The prop blades, for example, land under Thomas’ oversight—with their wide chord and downturned tips to dramatically reduce resonance and, thereby, noise.
“We design and make everything inside the airplane here,” said Wagner, as he kicked off our walk-through of the Santa Clara facility. “Six years ago [in 2017], we flew the first full-scale airplane, and coming out of that experience, we realized that, OK, this airplane works, the concept is solid, and we could architect the business. We made a really important decision—it was right around the time I was joining—that we were going to build up an engineering team to design and manufacture all of the electronic equipment in the plane.
“It started with a discussion about batteries and progressed [to] talking about motors, talking about actuators, talking about all the flight computers, things like that.”
Joby’s founding members decided to hire the team—design, manufacturing, and testing engineers— to create each critical component.
“When you buy something from a vendor, you’re gonna get whatever they have, with maybe some small changes to fit what you need,” said Wagner. “And when you design it yourself, you’re going to get exactly what you need.”
That takes enormous investment and engineering bench depth to pull off—that’s why so many OEMs work with vendors for a long parts list in the construction of an airplane. But CEO JoeBen Bevirt planned to vertically integrate Joby to that level from the beginning.
How They Got Here
Though the company boasted more than 1,000 employees around the time of our visit—and keeps growing daily—it still feels like a startup. The origin stories encased in various discarded components and updated blueprints lay around in plain sight. We stop in a showroom that’s between engagements, but it still houses one of the iterations of the fuselage and the cockpit and cabin contained therein. The moves Joby has made to determine the best combinations and materials for the interior and exterior it calls “explorations,” and posters walking back through those imaginings line a wall behind the mock-up. It’s like they’re not quite ready to put these pieces in storage yet, because they may gain use or traction somewhere down the line.
Following that experimental phase, the last seven years have been the more traditional aerospace development path, with requirements-based design “fit for purpose.” From scratch, it builds all of the battery packs for the airplane, the motors, and all of the electronics. “With the exception of the pilot interface—that’s the Garmin, we purchase that from Garmin, the displays—but all the rest of the avionics and electronics we build,” Wagner said.
Cruisin’ Down the Coast
Schedules kept us from hitching a ride with Bonny Simi, now president of air operations for Joby, in the Cirrus SR22 it operates. But we made our way nevertheless to the primary production and assembly and flight test operation in Marina, located on the airport there in a series of massive white Quonset hut-style tent hangars—that echoed in a way reminiscent of the big historic hangar at Moffett Field to the north, when it housed the dirigibles and other experimental aircraft in development. Fitting.
Once there, we were going to meet up with Didier Papadopoulos, head of the aircraft OEM for Joby, and the one responsible for much of what was going on inside those hangars. Instead—because we were there right after Memorial Day, our own scheduling concern, we had the next best thing, Scott Berry, a nine-year veteran of Joby. He’s also, tall, ranging, with a preternatural goodness and health emanating from him that feels like a trademark here. Berry has also built a Lancair Legacy and posts an AirCam on his LinkedIn profile. Taking aviation into an innovative direction feels like a natural fit.
“I had this dream that I always wanted to fly a seaplane into this area [Santa Cruz Wharf] and bring my children in and surfboards, put out an anchor, and then fly away,” Berry said. “I literally did that yesterday [in the AirCam on floats].”
The Joby aircraft will take this concept up another notch.
“I got my job because I had started my own eVTOL company,” Berry continued. “I was working for General Atomics…and I always wanted to develop my own aircraft. I was trying to convince General Atomics to do a version of the Predator drone with electrics…and I couldn’t do it, so I started my own company. I came to try and sell my aircraft to [Bevirt while on a holiday in Santa Cruz], and he convinced me to come work for Joby.”
Berry has spent the last nine years developing the design and certification team, running flight tests, and leading the company’s establishment of culture. That’s a critical element when what you’re doing is constantly pushing the human-machine interface—to watch the “human” part of the equation.
Humans and Robots
The production line order was still a bit out of sequence during our visit. At every turn, the interface between man and machine took center stage. We expect the use of robots in a variety of roles in manufacturing—and with Joby, they have been integrated from the beginning. Those integrations resonate in aerospace, but much of what I saw around me has roots in automotive manufacturing. Early on, Toyota invested in the company, and a significant part of its investment lay in the dedication of teams of Toyota colleagues embedded within Joby’s research and development—and that pattern continues as it transitions to production. But wait—it isn’t the same as a traditional transition from R&D and prototyping to building a conforming, deliverable model. Joby has been building the production line as it has developed the string of prototypes, so it would be ready as soon as the final fix was in to start production. That’s what we saw.
First, we toured the composites manufacturing facility, where boxcar-sized automated CNC machines crafted parts and shepherded through components from raw materials to layup.
Then we moved into the next big white tent, through a pass-through, hangar-sized door, on to the assembly and integration facility, where those components would join together into the airframe.
About Lunch
Back to culture now. Douglas Aircraft Company pioneered the concept of providing holistically for its employees, in the supposition that if they were healthy, well fed, and well housed, that security would translate to better job performance, less sick leave, and fewer HR issues. In Joby's world, that means everyone gets fed, family style, at the Marina complex. But the shared tacos are just an indicator.
“The vibe at Joby is energizing and unprecedented in my career,” said Thomas. “Joby embodies a truly unique and interesting mix of talent, passion, energy, innovation, focus and a can-do attitude that is very pervasive.”
Watching It Fly
During that visit in late May 2023, we had a unique window open to see the conforming prototype fly. The production unit was nearing completion at the apex of the line (also under construction), and though we couldn’t talk about that at the time, we can now.
A small team of specialists hovered around the model, smiles illuminating the obvious pride it felt in being so close to the completion of this next critical stage. Our ability to walk around the unit gave us an opportunity to talk through in more detail how the prototype had evolved into the airframe that would be ready for the final flight-test program of the primary campaign to TC.
In parallel, other teams at Joby are working on the business and operational cases, figuring out how the initial run of aircraft will fit into the national airspace system. “We’re not trying to create segregated airspace,” said Bowles, “but to blend in, working heavily with ATC in key regions that are in the initial target, i.e. [helicopter] routes in New York and LA.”
At the state and local level, the question is, are communities excited and ready? The low-noise profile helps immensely—at 65 dBA at 100 meters away on takeoff (vs. 93 dBA for a traditional helicopter liftoff) and in cruise down to 45 dBA—barely recognizable over the wind noise, as we discovered on the ramp in Marina.
It’s a “very torquey motor” in Bowles’ words, to turn the props slowly enough, with a big chord, so efficient at low rpm; plus a drooped tip lowers the vortex a blade length; plus five blades, with their angle of incidence not common to each other. The arrangement is such that it doesn’t stand up a resonance—so no sine wave and its resulting noise footprint.
As the teams look at every geographic location as a special case—procedures are always local—they assess the existing infrastructure—airports, helipads—and, over time, the development of a vertiport: a 50-foot piece of concrete with electric charging and noise limits.
Joby already can make use of the roughly 5,080 GA airports in the U.S. but adds 5,000 more heliports. That’s a lot of opportunity already in place if we can keep those landing sites open. With most people living an average 16-minute drive from an airport, that future lies in clear sight.
These columns first appeared in the March 2024/Issue 946 of FLYING’s print edition.


Sign-up for newsletters & special offers!
Get the latest FLYING stories & special offers delivered directly to your inbox