A Peek Behind the Scenes of Repair Station Ops
A visit to Aircraft Accessories International provides insight into the process of returning an aircraft to service.
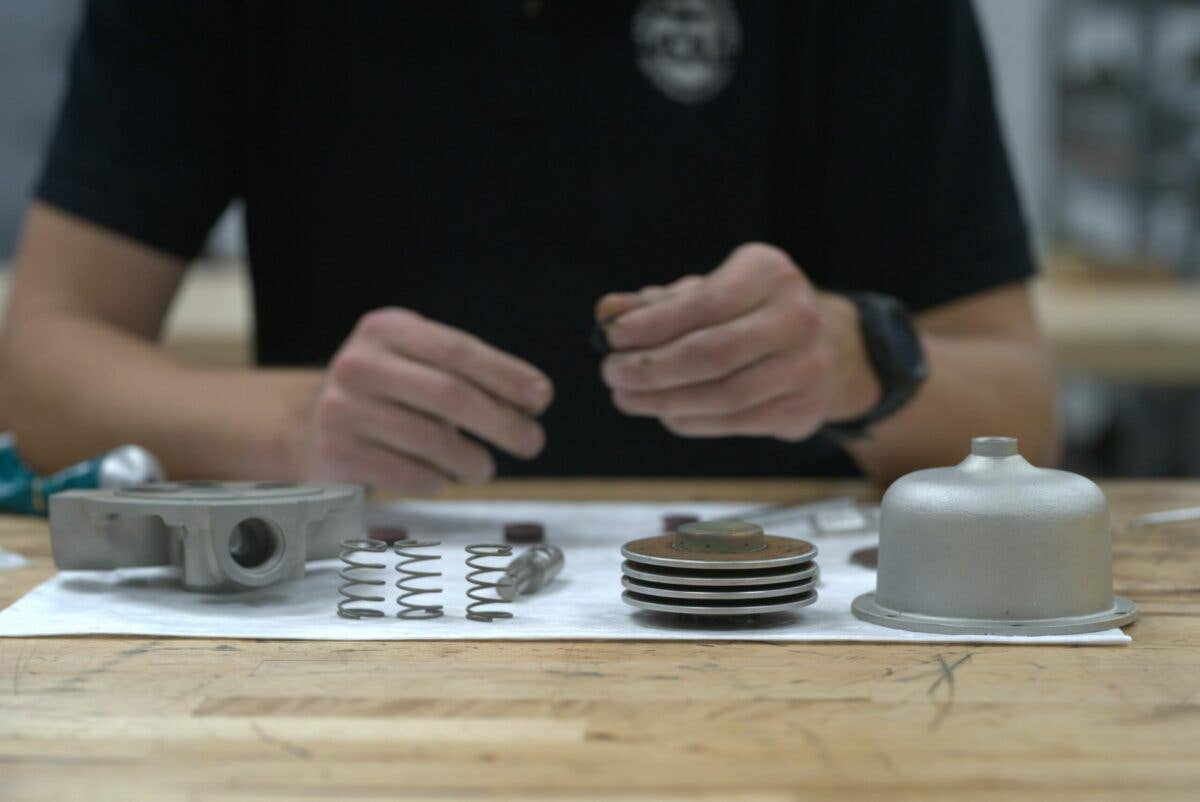
Aircraft Accessories International (AAI) specializes in accessory repair and overhaul for King Air components. [Courtesy: AAI]
There is a time in every aircraft owner's life when they hear an utterance that sends a chill through their entire body—and their checkbook. “Hey, boss. I think we have a problem with Four Six Echo.” Mechanics typically identify aircraft by the last three places of the N-number, and any A&P worth their salt will always use the phonetic alphabet.
In our example, Four Six Echo is the company’s Beechcraft King Air scheduled for a trip to close a big deal with a client in Oklahoma. Upon doing the walkaround, the copilot noticed a pool of hydraulic fluid on the ramp just next to one of the main tires. Not good. Hydraulic fluid belongs in the airplane's actuators, reservoirs, and hydraulic lines, not on the ramp.
After reviewing the logbooks, the director of maintenance determines that several key components are due for inspection. The team tried getting a few more flight hours before pulling off the parts. Nevertheless, it was time to pull the aircraft into the hangar and start jacking it up.
Before You Call
In FLYING Magazine Issue 943, I introduced you to a Part 145 certified repair station. Aircraft Accessories International (AAI), #VJYR666L, sits adjacent to Atlanta Regional Airport-Falcon Field (KFFC) and specializes in King Air component and accessory repair and overhaul. Founded in 2014, AAI began servicing one product, dry air vacuum pumps, and now service parts for Beechcraft, Cessna, Piper, and Bombardier platforms.
AAI is well-versed in consultative collaboration concerning aircraft maintenance. It recently published a blog entitled “Aircraft Maintenance: Landing Gear Actuators and Gearbox Transmissions.” The blog outlines some simple preventative measures to use when servicing the King Air. In the case of Four Six Echo, the time for preventive maintenance has passed, and it’s time to spring into action.
AAI president Kevin Allen discussed the repair process and the information the customer needs to have handy before making the call. Here are a few:
- What is the make, model, and year of the aircraft?
- Is this part incident-related (For example, did the plane crash?)
- What is the squawk? And try to be more descriptive than “it is inop.”
- What is your desired turnaround time (TAT)?
- Are there any maintenance restrictions to PMAs or DER repairs?
In “Maintaining Out-of-Production Aircraft,” I mentioned both parts manufacturer approval (PMA) pieces and designated engineering representative (DER) repairs. Let’s dive deeper into these solutions with AAI as our guide.
Both PMA and DER solutions can come in very handy if you are allowed to use them. Some maintenance programs forbid their use, typically because of service agreements by the OEMs. The bottom line is they prefer to sell new parts.
Once you have settled on the viability of alternate solutions, ensure the customer service representative (CSR) knows this. It could save you time and money. They may not be necessary, but once you build rapport with the shop, it will go out of its way to support you. An initial estimate gets the ball rolling, and it's time to ship the part.
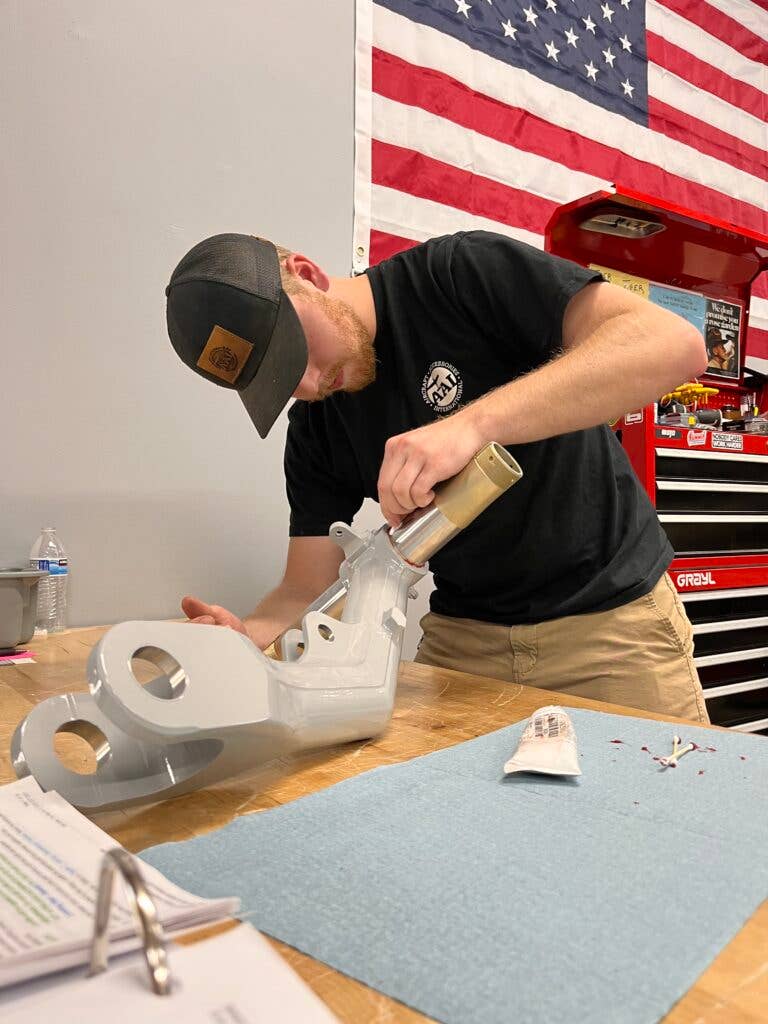
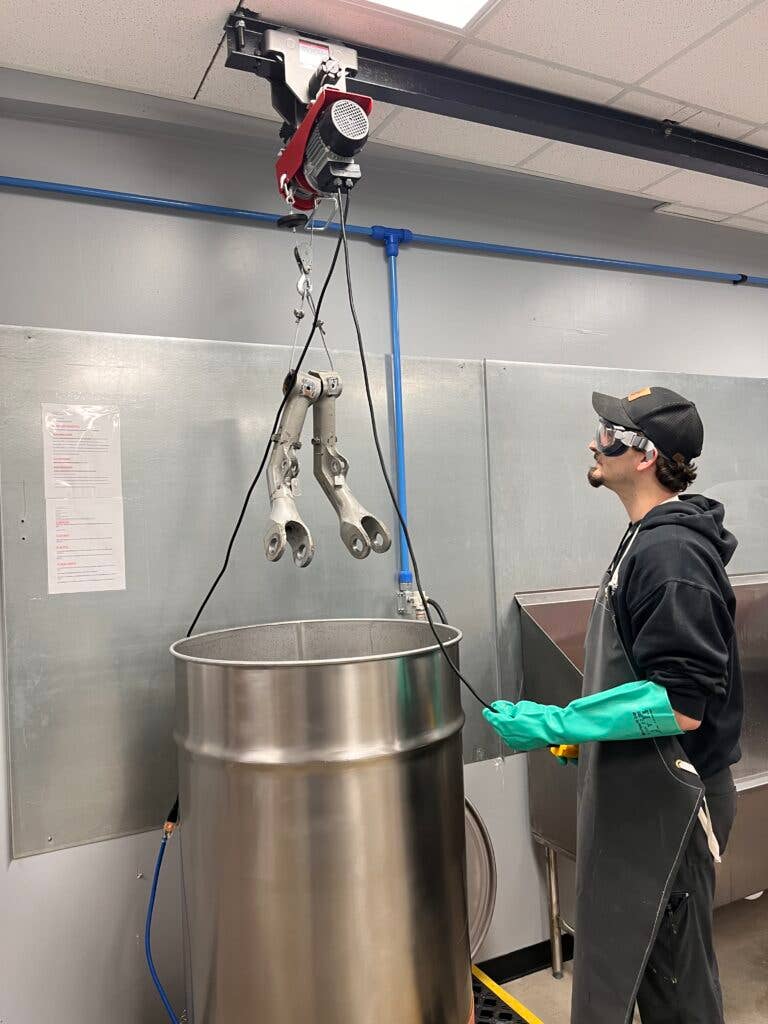
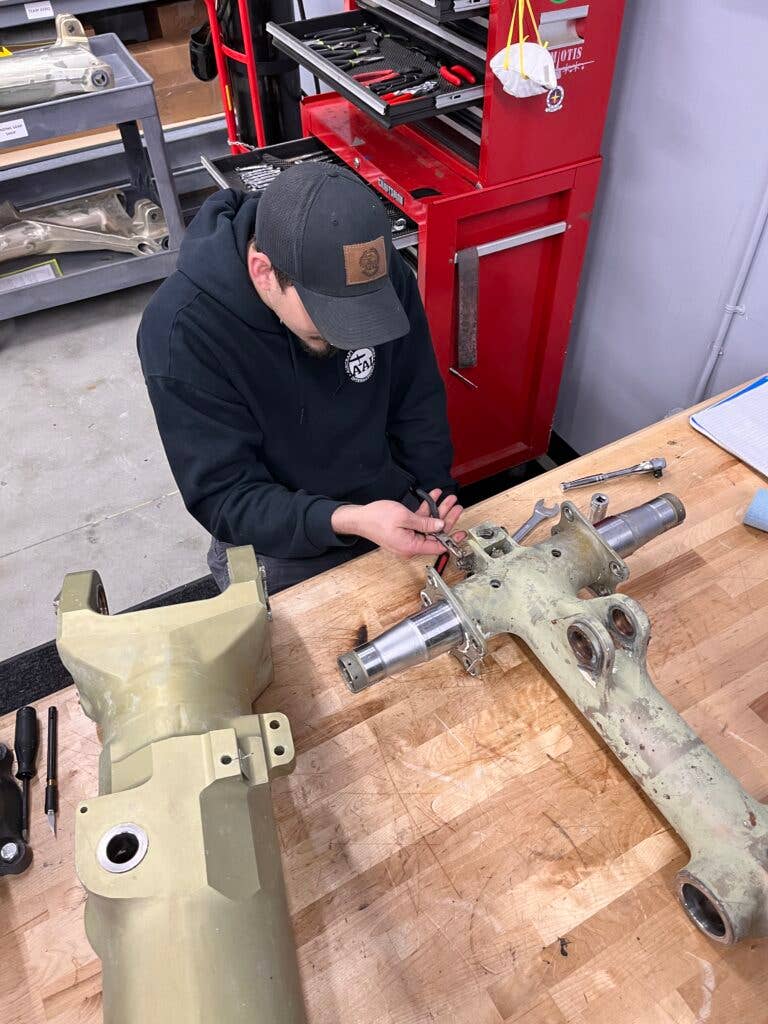
During the Visit
When a unit arrives, the receiving inspector removes it from the shipping container and begins to visually inspect the item for obvious defects and abnormalities. The data plate of the part is cross-checked against the packing slip or purchase order. Putting some form of statement of work (SOW) and contact information is imperative. If you just need the unit cleaned and tested but not worked, you better spell that out in plain English, or the shop may take it apart.
If the unit does require overhaul, the inspector will route to disassemble the unit and then on to cleaning. Once cleaned, the technician will dispose of the expendable parts, such as standard hardware, safety wire, and used fluid caps and plugs. A detailed inspection ensues, producing a bill of material (BOM). The CSR then compares the BOM to the original estimate. If everything checks out, they are good to go. If the unit requires additional items, it is time to have a conversation.
Once the CSR quotes the additional items, it is decision time. For example, let’s talk about the gearbox housing itself. This subcomponent would not be part of the original estimate, as the housing is not a normal failure item. How much does a new housing cost from the OEM? Does it have stock? Is there a PMA on the market? Most likely not if this part is not a common failure. Have you considered a DER repair? The shop can also write a repair specification to incorporate an alternate solution that could save the part from going beyond economical repair (BER).
AAI has numerous repair specifications in its arsenal. Essentially, it creates its own technical data, approved by the FAA and specific only to its repair station. Would you like to know more about this solution?
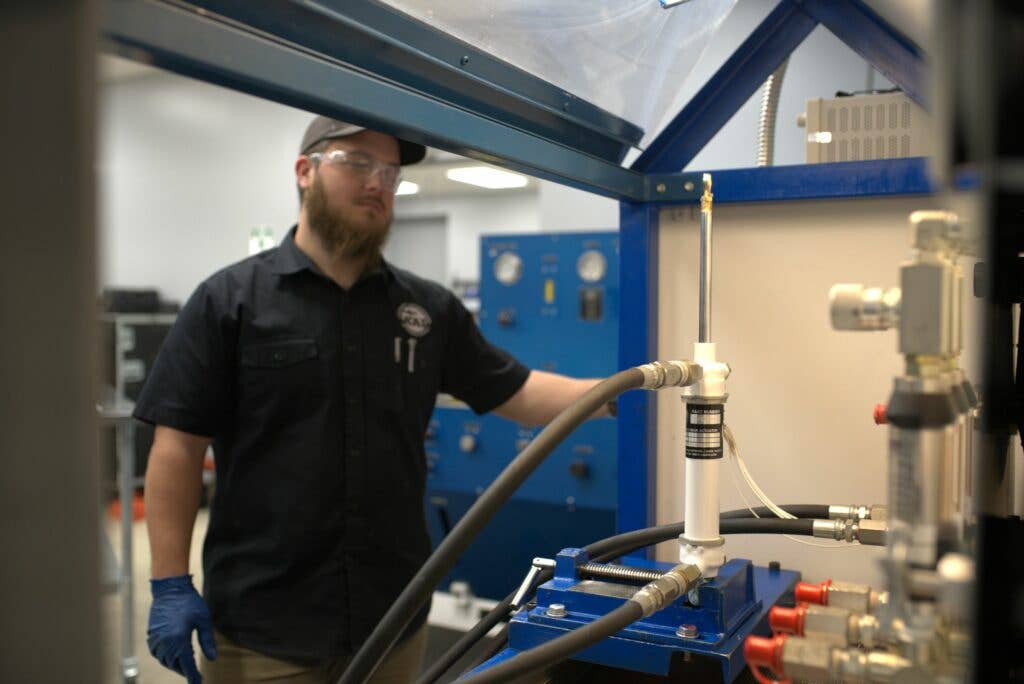
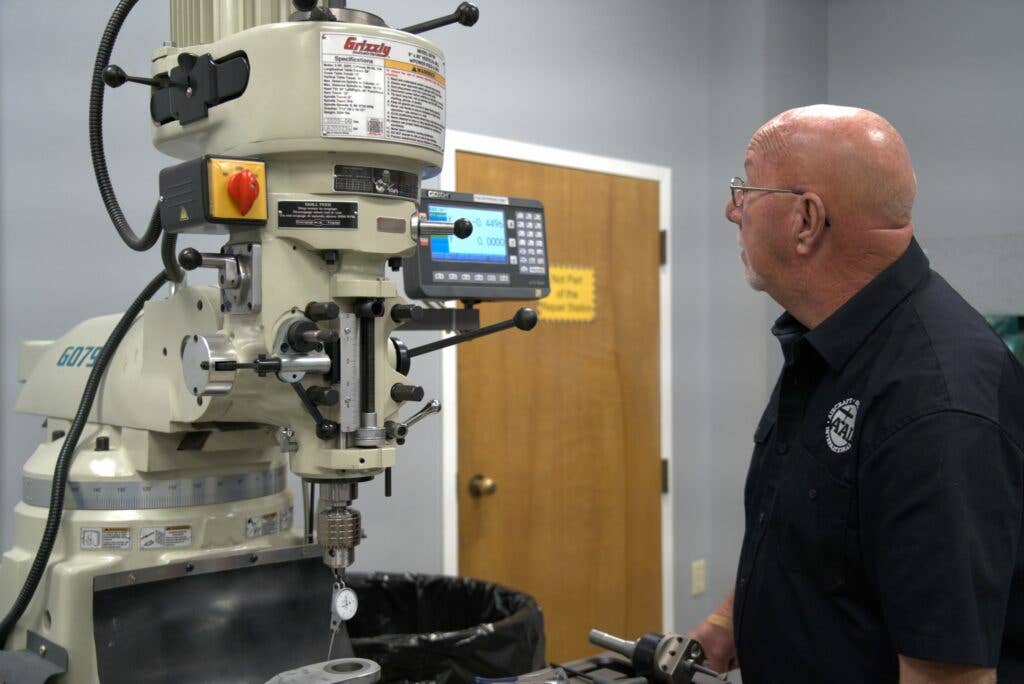
Returning to Service
Good news: The gearbox is on the assembly bench and should be ready to go in time for the next flight to Tulsa. Once complete, it will go through a series of tests, checks, and final inspections to ensure everything functions properly—and with no leaks.
It is important to follow correct maintenance procedures once you receive a unit from the overhaul facility. First, check the box it was shipped back in for damage or stains that could indicate a leak. If there is an issue, let the shop know right away. There is not much it can do for you if you call three months later with a shipment issue.
And lastly, follow all installation and testing parameters to the letter. The steps are in place for a reason. Failure to comply could result in loss of warranty or, worse, damage to the part or other parts in the system.


Sign-up for newsletters & special offers!
Get the latest FLYING stories & special offers delivered directly to your inbox