Bede XBD-2: Experimental Prototype for Unique Technologies
The clean-sheet aircraft design sought to improve aerodynamics by incorporating its twin engines in the aft fuselage.
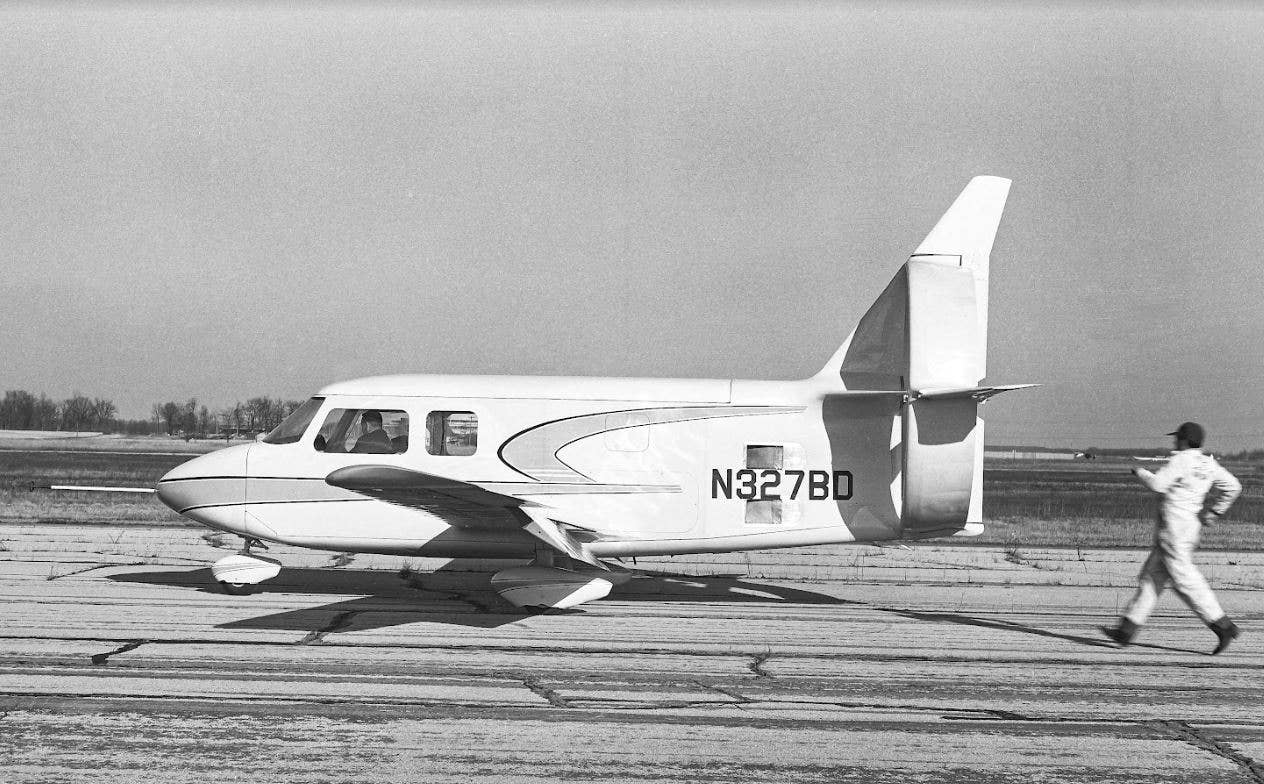
An undated slide showing the unique Bede XBD-2 during testing. [Courtesy: Jason McDowell]
Most aircraft engineers, tasked with designing a new STOL aircraft, wouldn’t opt to drill 160,000 holes in the wing and utilize two piston engines to drive a single pusher propeller.
But then again, most engineers aren’t Jim Bede.
While still enrolled in the aeronautical engineering program at Wichita University, Bede designed an aircraft that would incorporate a number of unique technologies. His vision was to integrate these technologies to provide superior performance to existing designs. Integrating new systems and complexity into an entirely new aircraft design, however, would prove to be challenging even for him.
Bede started with an entirely clean-sheet design. Envisioning an eventual family of multiple aircraft varying in size and passenger capacity, he began with an experimental prototype of the Bede BD-2, which he called the XBD-2. Intended as a proof-of-concept and testbed and first flown in July of 1961, it was boxier and more utilitarian than the sleek, streamlined concepts he endeavored to build, but it would function well for its intended purpose.
At first glance, even an experienced pilot or engineer might not guess the XBD-2 is a twin-engine aircraft. But it is, and two 145 horsepower six-cylinder Continental O-300s are snugly nestled in the aft fuselage, stacked one above the other. While such an engine configuration is decidedly unconventional, Bede was of the opinion that it offered several advantages.
Most obviously, housing the engines within the fuselage provides for a clean wing, undisturbed by engine nacelles and far more aerodynamically efficient. From a controllability perspective, an engine failure would be a non-event, as there would be no risk of asymmetric thrust. The lack of engine nacelles helped to reduce overall drag, enabling an 18:1 glide ratio.
A system of 10 belts and multiple clutches enabled operation at any combination of engine power, and the pilot could shut one engine down completely to maximize endurance. Bede even mounted each engine on a slide-out rack, a design he claimed enabled an engine to be removed in only 30 minutes. Presumably, little time was required to decouple an engine from the system of drive belts.
It was a complex system, but Bede wasn’t finished. With the assistance of Mississippi State University’s aerophysics department, he introduced further complexity to the aircraft by integrating a Boundary Layer Control, or BLC system, into the design. Utilizing 160,000 strategically-placed pinholes in the upper wing and aileron surfaces—holes roughly 30-50 percent as large as those in a typical air hockey table—the system would draw air into the wing to create additional lift. By causing the boundary layer to stick to the wing at high angles of attack, the system effectively increased lift and lowered the stall speed.
The BLC system drew air into the wing via a pump driven by the propeller shaft. So long as the propeller was being turned by at least one engine, the BLC system would operate. Ingested air was ducted back to the engines to provide additional cooling. The system proved to be effective, lowering the stall speed from 64 mph to only 42 mph—an impressively slow speed for an airplane with a gross weight of 3,300 pounds. Bede even claimed that the system would be undeterred by rain.
The most visually notable feature of the XBD-2 is the shrouded propeller. Bede was of the opinion that the aerodynamics at the tips of a standard propeller was one of the greatest sources of inefficiency, and he claimed his testing found that “a correctly-designed shroud” would increase the static thrust of a given propeller by over 100 percent. While many would be interested in seeing figures to back up this rather extreme claim, his other claim that a shroud greatly reduces propeller noise is perhaps more palatable and easy to accept.
The basic performance figures of the XBD-2 are impressive. At 9,000 feet, max cruise speed was said to be 179 mph at 16 gallons per hour. Max rate of climb at maximum gross weight was listed as 1,050 feet per minute with both engines operating and 720 feet per minute with one engine shut down, and the service ceiling was 21,000 feet on two engines and 14,500 feet on one.
Takeoff distances were similarly impressive. While the company didn’t specify at what weight the numbers were achievable, they claimed only 300 feet was required for the takeoff roll, and 500 feet was required to clear a 50-foot obstacle.
Ultimately, the XBD-2 logged approximately 50 hours of flight time before being permanently retired. No further derivatives were ever produced, and neither the BLC system, the coupled twin engine configuration, nor the shrouded propeller would make an appearance in any of Bede’s subsequent designs. Today, the sole XBD-2 is on display at the Manitowoc County Airport in Manitowoc, Wisconsin.


Sign-up for newsletters & special offers!
Get the latest FLYING stories & special offers delivered directly to your inbox