Boom Aerospace Delivers Update on Supersonic Model
The company announced new suppliers, and building the company’s ‘iron bird’ facility has begun in Colorado.
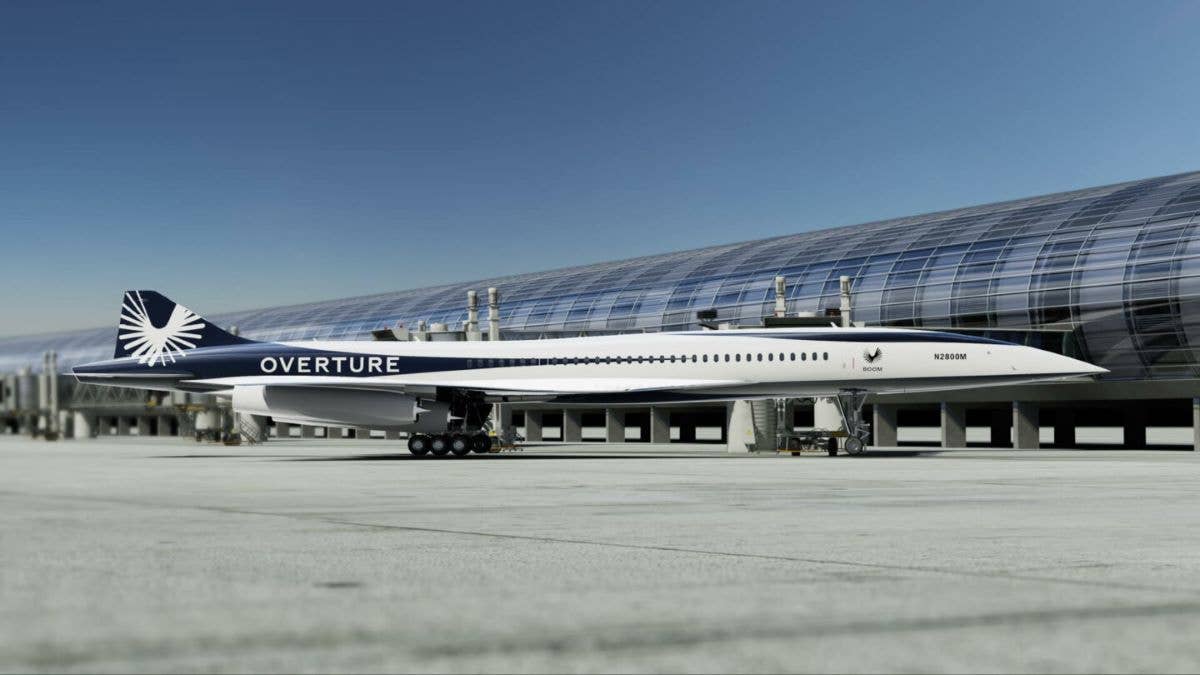
The Overture program continues on track with development progress on its proprietary Symphony engine. [Courtesy: Boom Supersonic]
Boom Supersonic’s collection of tier 1 suppliers now counts Leonardo, Aernnova, and Aciturri among the roster of global companies on board to develop and execute on the supersonic vision reiterated by Boom founder and CEO Blake Scholl.
The announcement was made on Tuesday at the Paris Air Show, along with several updates on the airframe and engine development as well as manufacturing and testing plans. The final product—the Overture—is projected to fly at Mach 1.75 in overwater cruise powered by bespoke Symphony engines running on 100 percent sustainable aviation fuel.
Mainline Suppliers
Leonardo, based in Rome, will provide its expertise in composite structure development and manufacturing as engineering lead for the Overture’s fuselage structural components integration, and serve as a design and build partner for fuselage sections—including the wingbox. The cross section of the Overture has a larger diameter at its fore section growing smaller towards the rear of the airplane. The design is intended to “minimize wave-drag and maximize fuel efficiency at supersonic speeds,” according to a statement from the company.
Aernnova, in Madrid, a large tier-one aerospace supplier, has been chosen to design and develop the Overture’s gull-shaped wings, which are structurally thinner than typical subsonic wings. Their nature is intended to reduce drag and increase efficiency at high speeds.
Aciturri, based in Miranda de Ebro, Spain, and another major tier 1 supplier, has been selected to provide the empennage to the Overture. A horizontal stabilizer that allows for greater control at subsonic speeds, including takeoff landing, is a key element to the tail design.
Symphony Engine Milestones
Florida Turbine Technologies (FTT) of Doral is the main partner on Boom’s proprietary engine, named the Symphony, and it continues to move forward in the two-spool, medium-bypass turbofan’s development. Scholl gave details on the powerplant’s specs along with teasing photos of the cross section that include the aforementioned optimization to run on 100 percent SAF. “Symphony features a high-specific-flow fan,” said Scholl, “which allows us to reduce the frontal area of the engine, which reduces supersonic drag.” Other details include:
- 35,000-pound thrust
- single-stage 72-inch fan
- air-cooled, multi-stage turbine
- FAA Part 33 and EASA CS 33 compliant
- adherence to ICAO Chapter 14 noise levels
Use of additive manufacturing will enable lightweight composition, low parts count, and reduced assembly costs. The engine features three low-pressure compressor stages, six high-pressure compressor stages, three low-pressure turbine stages, and a single high-pressure turbine stage. Former Rolls-Royce CTO and Singapore Aerospace programme chair Ric Parker serves as lead on the engine program, which has been under the magnifying glass when it moved away from former engine partner Rolls-Royce and went with a trio of new collaborators: FTT, GE Additive, and Standard Aero. Scholl spoke to this tangentially, stating that the need for a bespoke engine “specifically optimized for sustained supersonic flight and sustainable supersonic portions of that.” The vertical integration strategy is key to achieving this.
Manufacturing of the engines at scale will take place at FTT’s facility in Jupiter, Florida, Scholl revealed at the press conference. He also updated on progress of the company’s “iron bird” testing facility at its headquarters on the Centennial Airport (KAPA) on the south side of the Denver metro area in Colorado.
“This is the integrated test facility, where we will be able to put all of the systems hardware through exhaustive testing, with software and hardware in the loop, with thousands of simulated first flights before Overture makes its maiden voyage,” said Scholl. Flight controls, electrical power, and landing gear will all be operable in the iron bird facility.
Fuel System as CG Control
One of the unique aspects of the Overture includes systems architecture updated upon during the press conference by Scholl. While avionics, flight controls, hydraulics, and gear systems were touched upon—and will meet FAA and EASA Part 25 regs—he offered a bit of insight on the fuel system, which will be used to provide center of gravity (CG) control during both sub- and supersonic operations.
The all-composite makeup of Overture enables the use of complex aerostructures to create the contoured fuselage and gull-wing planform. Overall, the use of already certified technologies have been chosen thus far to reduce the risk on the program, as it breaks ground in significant ways in commercial passenger service.
The program remains on track in its 10-year development cycle—where it stands 3.5 years in—for a planned type certification in 2029.


Sign-up for newsletters & special offers!
Get the latest FLYING stories & special offers delivered directly to your inbox