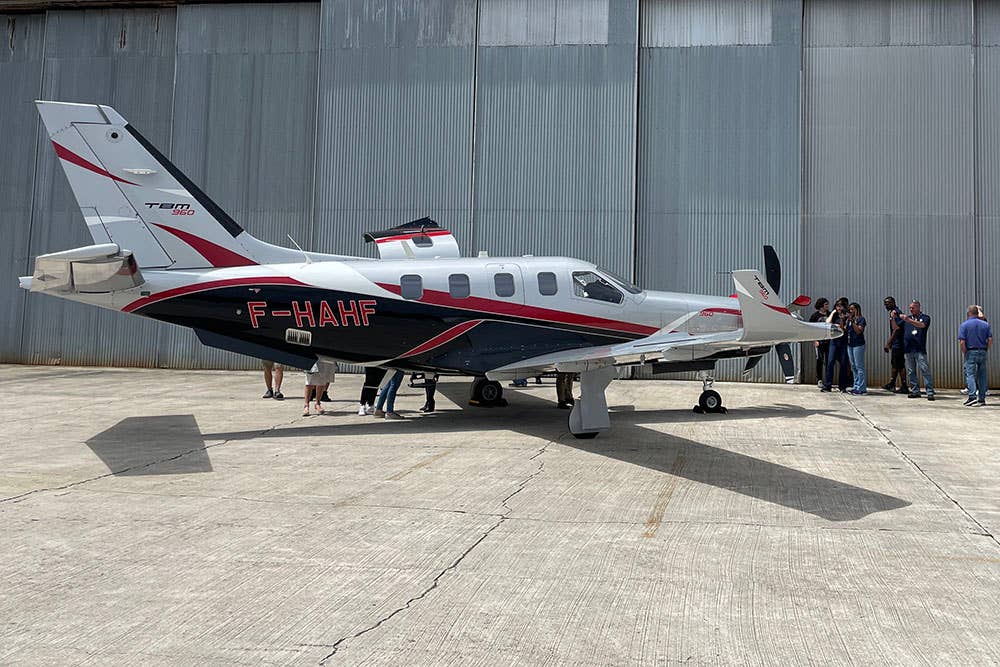
The newest Daher team members meet the newest TBM. [Photo: Julie Boatman]
In its quest to establish itself as a major international aerospace enterprise, including the addition of Boeing contracts to its portfolio, Daher has acquired an aerospace structures production facility in the U.S.
The plan to acquire Triumph Aerostructures in Stuart, Florida, was announced in February, as a complement to and expansion of Daher’s footprint in North America, as well as enhancing the company’s ability to serve customers, such as Boeing and Gulfstream, based in the U.S.
Senior leadership from Daher assembled on Wednesday with the entire Aerostructures team and local business leaders to celebrate the occasion. With a location map spanning 13 countries and 2021 revenue of $1.5 billion—including that of the new acquisition—Daher is completing its current five-year plan with a significant move to expand its reach in the U.S.
Didier Kayat, CEO of Daher, addressed this next stage at a press conference at the Aerostructures center.
“We were [before the Stuart acquisition] very Euro-centric, because…80 percent of the business was done in Europe, and we want to balance that and to do exactly the same business model in the U.S., in 15 years—or probably quicker because we have [experienced] the learning curve,” said Kayat.
In fact, he proposes that the company could accomplish the integration within five years based on what the team has learned. Daher produces aircraft parts and assemblies for Airbus (jets and helicopters), Dassault (including full fuselages), and Embraer, as well as its own TBM and Kodiak single-engine turboprops.
“We are the only company in the world that is an aircraft manufacturer as well as a family-owned company, as well as a company working in both manufacturing and services. I’m almost sure there is no company having the same DNA in the world.” Kayat estimated that 85 percent of Daher’s business is in aerospace.
Kayat also discussed how the company’s diversity of revenue streams helped it withstand the recessions of 2008 and the COVID-19 pandemic—and that the Stuart acquisition would further strengthen its ability to meet supply-chain demands as the aviation sector continues to rebound. “In 2009, we lost 20 percent of the business and recovery was done in two years,” said Kayat, “whereas the whole market suffered much longer than that. In 2020, with the COVID crisis, the whole market lost 40 percent of the business; we at Daher only lost 15 percent.
“We do consider that producing something without having security in the supply chain doesn’t make sense—that’s why we are also a big player in logistics and services, because we consider the discontinuity between the supply chain, the warehousing, the manufacturing, and the final assembly line are key in the success of what we do, and what we do for our customers.”
What Does It Build?
The personnel at Triumph have expertise in crafting complex structures for aerospace applications. These include building wing and fuselage assemblies—such as the massive center wing sections and paired horizontal stabilizers for the Boeing 767, and the far more delicate flap assemblies for the 777—incorporating not only advanced metal manufacturing and bonding processes but also thermoplastic and other composite layup capabilities.
The addition of the Boeing contracts gives balance to Daher’s overall customer mix in commercial aviation, which had been heavily focused on Airbus. The Stuart facility also makes a small volume of components—about 5 percent of the total production—for Gulfstream at the moment.
Advanced processes, such as 3-D printing of certain composite structures, have also been implemented on the TBM series, and this could be part of the future as well. “The idea of our technology department and the three tech centers [Daher has developed] is to test everything—and not only to test them but to use them on our own planes—we are the OEMs on that,” said Kayat. “And we can test and see what is reasonable to do, not just reasonable to buy.”
Laurent Schneider-Maunoury, senior vice president of industry for Daher, gave examples of metallic components Daher currently produces in Europe. “We are making some winglets, some main landing gear, wing boxes, total wings—for ourselves…but also for ATR, for Gulfstream, and for Airbus,” Schneider-Maunoury said. “You will find these types of products here in Stuart. There’s only one difference—the size. Here, it’s far bigger.”
The Stuart facility sits at a critical intermodal point, with its site on the Stuart airport, Whitman Field (KSUA), and a rail line coming into the factory. Ports at Cape Canaveral and Miami also lie within easy reach.
Creating the feeling of belonging is a critical part of the Daher culture. “For us it is very important, the fact that we are family owned,” Schneider-Maunoury said. “In the current Daher group, we are part of the same culture. When you bring someone in, you adopt someone—you make a sense of belonging.”
Schneider-Maunory looks forward to the integration and support the Stuart facility will bring to Daher’s Kodiak manufacturing currently taking place in Sandpoint, Idaho, as well as facilities serving Airbus and other OEMs in the U.S. A “complete, competitive supply chain” within North America is the goal, he said. However, the current capacity for manufacturing the TBM series at Tarbes, France, and the Kodiak in Sandpoint is sufficient, with some room to expand, according to Kayat.
A History of Manufacturing Integration
“As a family-owned company, our core strengths are built on a long-term vision and a corporate social responsibility policy that values our employees,” said Patrick Daher, chairman of Daher’s board of directors, in a statement. “We are fully committed to the Stuart facility’s future, and look forward to its role in serving our customer base as Daher shapes the aviation supply chain of today and tomorrow.”
The roots of Daher go back to 1863—the time of Napoleon III—while the aircraft manufacturing business that now builds the TBM and Kodiak series had its beginning in 1911, as Morane-Saulnier. “We always claim the milestones of the companies we acquire,” said Kayat, including this heritage that was adopted by Daher upon its acquisition of SOCATA in 2009.
Current family ownership stands at 87 percent, and the company will remain family-owned, as Kayat confirmed. “The advice I have from my shareholders is, ‘You can do whatever you want but you must always keep more than 51 percent of the company.’ And that counts because it helps us, having long-term vision strategies. We can invest in aerospace, [in] long-term programs.”
In It for the Long Haul
The fact Daher plans to make those long-range commitments to the Stuart team and the local area appeared to resonate with the employee group assembled for a town hall following the press conference and tour of the manufacturing lines.
General manager for the Stuart center Curtis Hoffman captured the feeling in his remarks. “As your site leader, I am very proud of everyone…As communications continued with Stuart and Daher, the synergy was evident, and I knew early on that Daher was a perfect partner for us.” Daher intends to keep current management in place at Stuart, as well as the potential to grow the workforce from today’s 400-person headcount.
Following our acquisition of the Stuart, Florida #aerostructures facility, we officially welcomed its 400 employees into the Daher family. Daher is now a Tier 1 supplier to @Boeing and we’ve increased our work for @GulfstreamAero. This is another milestone in our strategic plan. pic.twitter.com/u7lYj5Qt9n
— Daher (@DAHER_official) July 7, 2022
“The energy has been very positive ever since Daher started coming to see us,” Hoffman said. “The first thing Daher wanted to know from me was, ‘How are the people? What are the people like?’ It wasn’t about ‘Are you making schedule? What’s your quality?’ It was about people. So we knew right off the bat it was a family business, and we were going to be part of the family.”
Daher also plans to team with the local business community and city and county leadership on several fronts, including education, tapping into K through 12 schools and Indian River Community College for workforce development and inspiring aerospace careers.
Another aspect of the long-term vision lies in the commitment to decarbonization. With its EcoPulse demonstrator in development, Daher looks to show its leadership in the drive towards a net-zero-emissions air transportation environment by 2050.
“This is a demonstrator—not a product…we are learning a lot, with the help of Safran for the engines,” Kayat said, “and Airbus for the batteries, and we are providing the airplane. We are learning how to manage high voltage in a plane—because we are convinced that, being a family-owned company, that we have to be a responsible company, and accelerate in the decarbonization of our product.
“Otherwise, we lose the business…the younger generations, especially in Europe…are very keen on how [we can] limit the impact on the planet, and we have to be part of that.”
Those engines from Safran currently on the EcoPulse? They’re six distributed propulsion motors mounted on the wing’s leading edges and tips of a TBM-based airframe. Kayat projected that the EcoPulse would make its first flight by the end of 2022.
Another piece of Daher’s environmental approach? Going back to testing in 3-D printing, the company is investigating in its tech centers the recycling of thermoplastics in that model. Utilizing scraps of plastic from the components it manufactures for customers, Daher has produced new parts as part of the testing.
Daher Delivers First U.S. 960s
Daher’s senior vice president of the Aircraft Division, Nicolas Chabbert, flew one of the new TBM 960s to Stuart from the company’s service center in Pompano Beach (KPMP) so that the new Daher team members could get a look at this important member of the family. Daher obtained FAA certification for the aircraft on June 24, on top of its EASA approval back in March.
The first two 960s with FAA airworthiness certificates came across the pond starting on June 25 from France for customer acceptance at Elliott Jets, based at Flying Cloud Airport (KFCM) in Minneapolis, Minnesota, and AVEX Aviation at the Camarillo Airport (KCMA) in Southern California.
“I want to recognize the collaborative work of EASA and the FAA that resulted in the TBM 960’s certification,” said Chabbert. “I also want to express my thanks to our U.S. customers for their patience during the certification process. We’ve had an exceptional response overall to the TBM 960 since its launch, with more than 60 orders now logged worldwide for this latest version.”
Chabbert confirmed that a total of nine TBM 960s had arrived in the U.S., with 10 delivered thus far in Europe. Plans include a total of 60 TBM deliveries in 2022.


Sign-up for newsletters & special offers!
Get the latest FLYING stories & special offers delivered directly to your inbox