Entering a Hangar-Hungry Market
A construction team in the Pacific Northwest is putting the finishing touches on a new GA development featuring 14 T-hangar units.
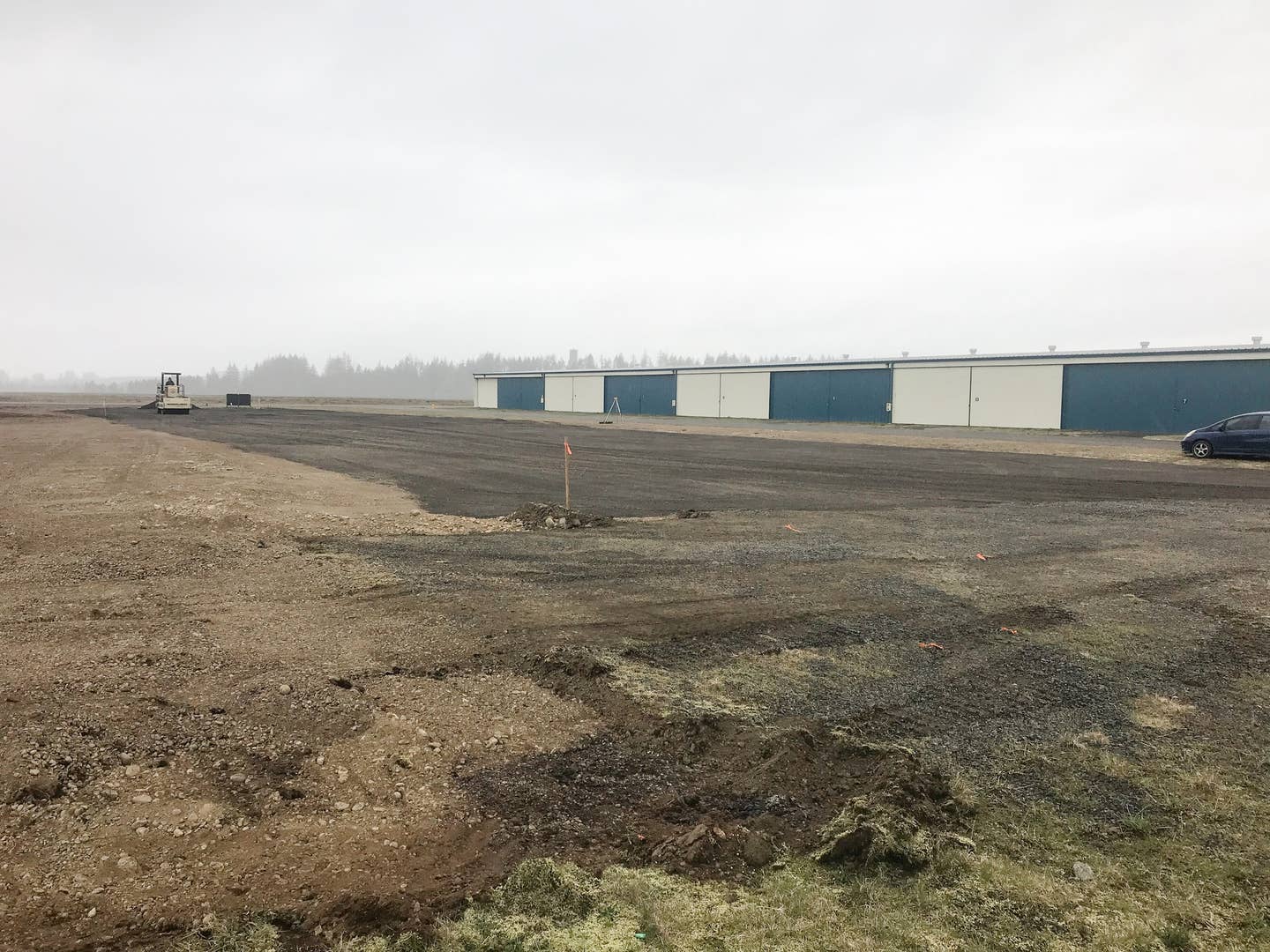
Fourteen new T-hangar units are being built at Sanderson Field Airport (KSHN) in Shelton, Washington. [Courtesy: Shelton Condo Hangar 91]
Pilot needs for hangar space in the Pacific Northwest—hampered by limited supply—has become a business opportunity for a Washington state construction company.
“Tim Jahner, my partner, owns Jahner Built Construction, and originally he started building airplane hangars for a skydiving operation up here in Shelton, Washington, on a private airstrip,” said Austin Larman of Island Lake LLC. “Tim built the hangar for them, and I did all of the electrical work, which is how the two of us got to know each other.
“Then Skydive Kapowsin asked if we would build another hangar for them at Sanderson Field Airport (KSHN), as a place where they could do maintenance for all of their skydiving airplanes. We did that, and then we built three corporate box hangars here at the airport for separate owners.”
Demand for their services in the area made it an easy decision for Larman and Jahner to make a case for starting a hangar construction business.
“After the third box hangar, Tim and I talked about what’s next,” Larman said. “I told him that I was going to start building T-hangars because there is a need for them. I had been talking to a lot of folks who were thinking about doing the same thing, so after a few conversations we decided to partner, and that’s when we formed Island Lake LLC close to three years ago.”
The team entered the hangar-hungry market at just the right time. The reception from local pilots has been positive to the new space offering.
“There were probably 60 people on the waiting list at the airport at the time we started this process,” he said. “And we didn’t just go to KSHN to see what the waiting list was like there. We looked at other airports in the area as well. I went to Olympia. I went to Bremerton. I went to Chehalis. I went to Toledo and every other regional airport within a hundred-mile radius, all of which had anywhere from 40 to 120 people on their waiting lists.”
The company is currently putting the finishing touches on a new GA development in upstate Washington. The 21,000-square-feet Shelton Condo Hangar 91 project consists of 14 T-hangar units.
“It took us almost two years to do all of the environmental studies and work with the Port of Shelton for a land lease on the acre and a half parcel,” Larman said. “We just broke ground in April this year and are set to finish up the project in the next six to eight weeks, with tape and mud, as well as painting and installing fixtures left before the final survey is completed.”
New hangars call for the opportunity to develop furnishings that better meet the needs of aircraft owners than existing structures. As such, the team took a great deal of operator feedback into consideration when designing the units.
“Pilots told us that standard 12-foot-by-40-foot doors aren’t big enough,” Larman said. “On their request, most units have 14-foot-by-44-foot doors, and two have 46-foot-wide openings for people with wing extensions or larger aircraft in general. There are three different unit sizes, ranging from 1,360 square feet to 1,864 square feet a piece. All units are fully insulated, and we are doing radiant heated floors. We have four boilers that will feed all 14 units, each with their own manifold.
“So, if a condo opens their hangar, their manifold shuts off while the door is open. The units have more outlets than you need, 50-amp subpanels, LED lighting, and individual fiber for internet. There are Schweiss bifold doors with auto locks and two remotes—one for your car and one for your plane.”
- READ MORE: One Man’s Rally to Keep an Airstrip Alive
The market dynamics appear to be ripe for more private organizations to develop hangars for government-owned and managed airports.
“The hangar shortage is a problem in most places nationwide,” Larman said. “This was clear once I started talking with people from other states. I have had many conversations with municipal airports about how they can’t pencil it out to make a hangar development work, because of the costs. Since they must pay prevailing wages as a government agency, the math doesn’t add up to make it feasible, so they must rely on private individuals to come in and invest into these airports.”
The Island Lake team plans on continuing to invest at Sanderson Field, as well as other airports where it can have a positive impact.
“Right now, we are trying to get the airport’s master plan changed because we have 10 more acres that we have the first right of refusal on, that we performed environmental studies on,” Larman said.” So, we are hoping to build more box hangars and more T-hangars here after completing this condo project.”


Sign-up for newsletters & special offers!
Get the latest FLYING stories & special offers delivered directly to your inbox