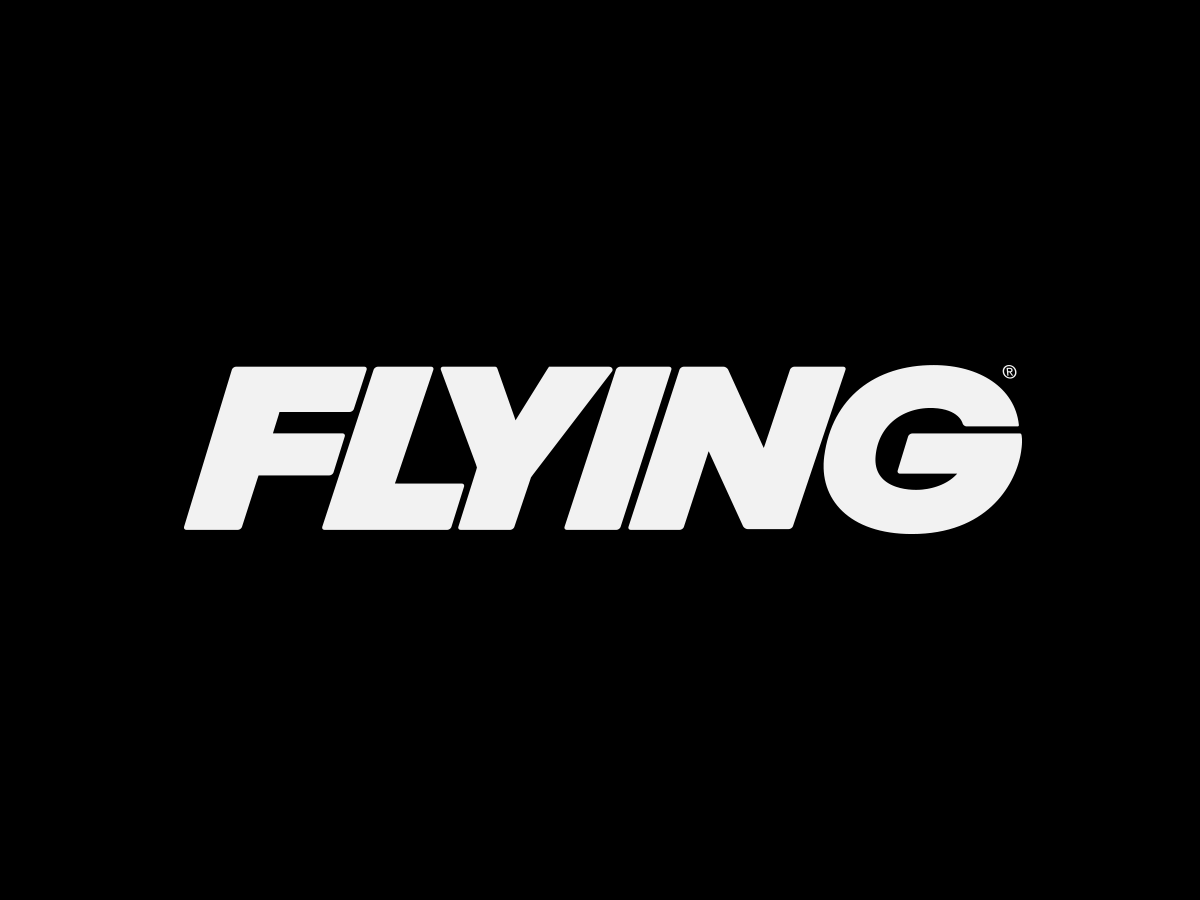
The November 2001 crash, shortly after takeoff from JFK, of American Airlines Flight 587 sent a tremor through the aviation community. It involved an extremely rare event: the structural failure, and complete separation, of one of the major flying surfaces-namely, the vertical stabilizer-of the airplane, an Airbus A300-600. In the ensuing loss of control, the engines also broke away from the airplane, which crashed on Long Island killing all 265 persons aboard.
According to the National Transportation Safety Board's recently published report on the accident, only one other commercial airliner, a Boeing 707 that broke apart in severe turbulence near Mt. Fuji in 1966, has ever lost a fin in flight from external causes. That 707 encountered mountain wave turbulence so violent that the airplane broke into a number of pieces before reaching the ground, and a U.S. Navy aircraft sent to investigate encountered gust accelerations far outside the flight envelope of any airliner. In the case of the Airbus, however, extreme turbulence was not a factor. The closest thing to it was the wake of a 747 five miles distant. Such a wake can give even a large airliner a pretty good thump, but cannot tear it apart.
The finding of the NTSB was that the first officer, who was the pilot flying, used inappropriately vigorous, rapidly alternating rudder inputs in response to the wake encounter. Normally, jet pilots stay off the rudders; but this particular pilot, according to one captain who had flown with him, had shown an inclination to overuse them. (On the other hand, some described him as an above-average pilot who never flew airplanes aggressively, but rather "smoothly and accurately.")
Two other factors were thought to have contributed to the overcontrol. One was the design of the A300-600's rudder control system, which provided very little force feedback. In fact, the additional force needed to drive a pedal to its stop at 250 knots is less than the 22-lb breakout force-intended to prevent inadvertent rudder movements-needed to move the pedal in the first place. A survey of airline airplanes found none with rudder forces lower than those of the A300. Most other Airbus models, however, including the big four-engine A340, have characteristics similar to those of the A300-600, while Boeing and McDonnell-Douglas models without exception have lower breakout forces and considerably higher deflection forces.
Airbus had deliberately reduced the rudder forces when it developed the A300-600, as compared with the earlier A300B2/B4, in order to keep them in harmony with reduced roll forces. It also replaced the earlier model's variable-ratio rudder travel limiter (which allows less and less rudder travel in response to the same amount of pedal travel as speed increases) with a simpler variable-stop system. One of the consequences of the change was that as speed increased, the pedal travel shrank and the force required to achieve the maximum allowable rudder deflection decreased. In effect, the sensitivity of the rudder pedals increased with speed. The fleet standards manager of American Airlines' Airbus 300 fleet told the NTSB that he "did not think that any pilot would have thought that full rudder could be gained from about 1 1/4 inch of pedal movement and 10 pounds of pressure (above the breakout force) at an airspeed of 250 knots."
Another possible contributing factor, according to the Board, was a simulator routine intended to train American's pilots for recovery from upsets. One demonstration case required a bank angle of more than 90 degrees, but the simulator could not be made to reach that angle if the pilot reacted promptly when the upset began. The simulator was consequently reprogrammed to make it unresponsive to rudder until it attained the extreme bank angle. This artificial suspension of rudder effectiveness, the Board thought, might have instilled in this first officer-and possibly in other pilots-a sense that the real airplane would be similarly unresponsive, and that swift and vigorous rudder action would be needed to arrest any incipient upset.
The most significant finding to emerge from the accident, apart from the stated probable cause, was that the FAA's right hand didn't know what its left hand was doing. The NTSB reported that the fin failed at a load more than one-third higher than that required for certification; thus, Airbus was blameless. Pilots, on the other hand, found it inexplicable that any aerodynamic load could cause a failure in an airplane flying under VA, the maneuvering speed. By and large, pilots believed that you can't break an airplane at or below VA. They had good reason for thinking so. The FAA's own "Pilot's Handbook of Aeronautical Knowledge" says that "any combination of flight control usage, including full deflection of the controls, or gust loads created by turbulence should not create an excessive air load if the airplane is operated below [the] maneuvering speed." FAR Part 25 contained a requirement that pilots be made aware that "full application of rudder and aileron controls ... should be confined to speeds below" the maneuvering speed-a declaration that does not state, but that most people would understand to imply, that such control applications below the maneuvering speed would not, incidentally, tear the airplane apart.
Various experts at American Airlines told the Board that they had always believed that VA provided absolute structural protection. American had, furthermore, incorporated into its "Advanced Aircraft Maneuvering Program," which was intended to teach pilots how to recover from upsets and unusual attitudes, the advice that rudder rather than ailerons/spoilers should be used in certain circumstances, together with the implication that unusual attitudes were most likely to occur as a result of wake encounters; but there was no guidance on the possible effects of rapid rudder reversals. Evidence existed that this program had had an influence on the accident's first officer's flying technique. Another document, the Airplane Upset Recovery Training Aid, prepared cooperatively by airframe manufacturers and a number of airlines, had also emphasized the use of rudder in unusual-attitude recoveries. Airbus had criticized it, not on structural grounds, however, but because unwary use of the rudder could lead to spins. Incidentally, Airbus also expressed doubts about the realism of simulators-another issue that would later play a part in this accident investigation.
The overstress protection that exists at VA is, in fact, limited; but even the FAA itself seems to have been confused about what kind of protection VA actually provides. It was as though the engineers who design airplanes, the bureaucrats who certify them, and the pilots who fly them existed in different worlds, separated by a membrane impermeable to information. But that isn't the case. Some pilots are aeronautical engineers, and all airframe manufacturers, and the FAA, employ pilots. Although they seem to have been news to the NTSB, no one can suggest that the misconceptions about VA that pervaded the flying community were unknown to the airframe manufacturers.
One of two steps needed to be taken. Either the manufacturers had to build their airplanes to match the beliefs of the users regarding maneuvering speed, not just the technical requirements of the FARs, or else some effort had to be made either to re-educate pilots or to re-define the maneuvering speed so that it would play the role expected of it. None of these steps was taken prior to this accident.
Current certification requirements for maneuvering speed assume the use of only one control at a time; for instance, they do not provide for simultaneous pitch-up and roll. Furthermore, as far as the fin and rudder are concerned, full rudder deflection is permitted only when no sideslip is present. In other words, if the airplane yaws you are not allowed to use full rudder to bring it back.
The aerodynamic concept underlying the FAR definition of maneuvering speed is a simple one. A flying surface can only provide a certain maximum lift coefficient before stalling, and the aerodynamic force experienced at that lift coefficient depends on the speed. The force exerted at the maneuvering speed is the so-called limit loading for which the wing structure is designed.
Nevertheless, that is really not the greatest force a wing can experience at the maneuvering speed. A limit-load pull-up combined with roll produces a still larger load, because the downward-deflected aileron, like a landing flap, increases the amount of lift the outer portion of the wing can produce while adding a large torsional, or twisting, component. Similarly, anti-yaw rudder applied when the airplane is in a sideslip-this was what broke the Airbus's fin-produces a larger load than the fin would experience with its rudder aligned. To be sure, it is difficult to apply full rudder against maximum sideslip, because the airplane begins to stabilize itself before the pilot can react. The theory, in the case of AA587, is that the pilot got into phase with the airplane in such a way that, with the help of the Airbus's unusually sensitive rudder pedals, he managed to apply full rudder at the worst possible moment. His case was not unique; the NTSB enumerated six previous instances of upsets in Airbus aircraft in which fin stresses had exceeded the design ultimate load. None involved the A300B2/B4 with the variable-ratio rudder limiter.
It might seem desirable to change certification requirements so as to require sufficient structural strength to withstand all control deflections in all attitudes at the maneuvering speed. Airframe manufacturers might resist such changes, however, because they would require heavier structures and thus raise the operating costs of future models, and would represent a massive and costly remedy for a statistically minor problem. An alternative to structural changes might be fly-by-wire control systems, which many Airbus models, but not the A300, already incorporate. Fly-by-wire systems can be programmed to hold structural loads within acceptable boundaries.
For existing aircraft, two changes could be contemplated. One would be to lower the published VA to a level at which all possible maneuvers are protected. If the loads experienced by AA587's fin be taken as a guide, the speed reduction would be on the order of 10 percent. Of course, even redefined V-speeds would not necessarily change the speeds at which airplanes are actually flown. AA587 was not flying at 250 knots in order to stay below VA, but to observe the speed limit below 10,000 feet. But they would make the meaning of VA more clear, and the implications of certain combinations of control movements more apparent to pilots.
The other change, which has already been set in motion by this accident and will continue, is to re-educate pilots about what VA means for airplanes that currently exist. Still, the most re-educated pilot in the world may forget what he knows if the airplane is flipped over at low altitude by a wake turbulence encounter, or when he thinks it's about to be.
This article is based solely on the National Transportation Safety Board's report of the accident and is intended to bring the issues raised to the attention of our readers. It is not intended to judge or to reach any definitive conclusions about the ability or capacity of any person, living or dead, or any aircraft or accessory.


Sign-up for newsletters & special offers!
Get the latest FLYING stories & special offers delivered directly to your inbox