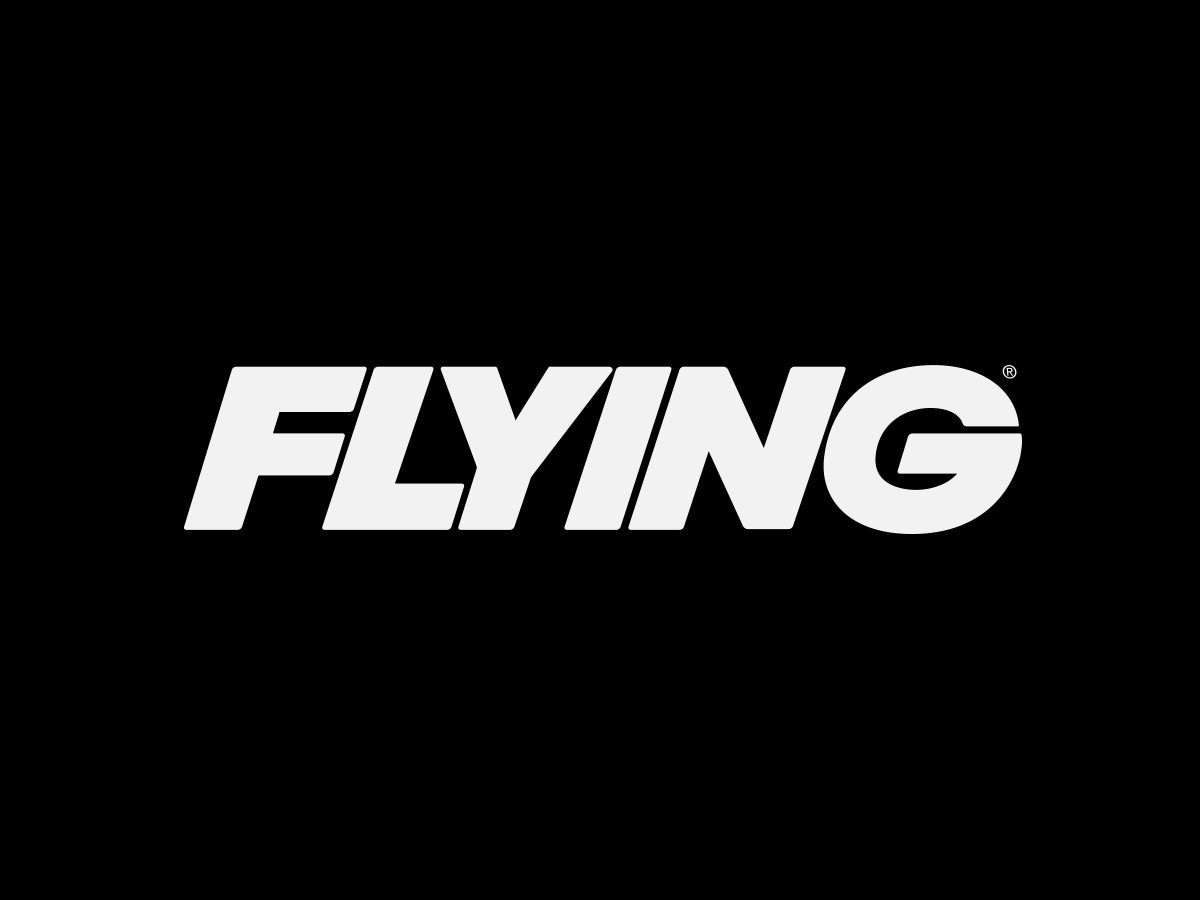
According to an eyewitness whose attention was caught by the loud gunning of its engine as it approached the airport, the little two-seater's wings both vibrated visibly before the left wing folded back against the fuselage. The airplane pitched downward and began to spin; the right wing then bent upward, and it too folded back against the fuselage. Moments later the airplane struck the ground and exploded in flames.
Two men were aboard: the 350-hour pilot-owner, who had bought the airplane from its amateur builder seven weeks earlier, and a 17,000-hour flight instructor. The airplane, equipped with a six-cylinder Jabiru engine of 110 hp, had been flown only 60 hours; this was its new owner's first outing in it.
It was an isolated incident — flutter, to all appearances, but without a clear cause that accident investigators could determine — until 10 months later in the same year, 2006, when a similar airplane experienced a similar in-flight breakup. Again, the engine was heard to rev. Some witnesses reported that it was sputtering or misfiring, but many airplanes produce an irregular exhaust sound at idle. Then there was a loud bang, and the airplane, according to one witness, "blew up," both wings separating from the fuselage, which rotated as it descended to the ground. The 79-year-old pilot and his wife were both killed.
Six months later, another airplane of the same type crashed in Texas. The weather was bad — low ceilings, heavy rain, nearby lightning — and the 176-hour sport pilot, the sole occupant, flew in the vicinity of the airport for 16 minutes before crashing 2.3 miles away. It looked like a straightforward VFR-in-IMC accident — the IFR-qualified owner of a 210 based at the same airport had declined to fly in the heavy rain, even though he had an urgent need to do so — except that the wreckage was spread out along a line 1.3 miles long, revealing that the airplane had broken up in flight.
The pattern of in-flight wing failures continued. In April 2008, a factory-built LSA version of the airplane crashed after its left wing broke "for undetermined reasons." In Europe that year, two kit-built versions of the airplane suffered similar fates. In March 2009, one broke up in flight in Utah; and in November of the same year another shed its wings in Arkansas.
There were no witnesses to all of the crashes. But what was noteworthy about the ones that had been observed was that the wing failures did not seem to involve aerobatics, rapid maneuvering or even high speed; the airplanes were in level flight. Reports of revving engines can possibly be attributed to efforts to "clear" the engines after a descent; at any rate, there was no suggestion that changes in engine power had anything to do with the wing failures. The most telling observation was that of wing vibration in the first 2006 accident; visible vibration invariably implies flutter.
The airplanes were all Zodiac CH 601s, a design by a well-known and respected aeronautical engineer, Chris Heintz, that is available both as an LSA and as a kit for amateur builders. Since 1998 the 601 has been produced by various concerns and individuals. A European firm, Czech Aircraft Works (CZAW), produced 750 of them; an American firm, Aircraft Manufacturing and Design (AMD), produced 117. Zenith Aircraft of Missouri sells plans and kits to amateur builders under license from Heintz's Canadian company, Zenair. Zenith, by the way, is an ingenious anagram of Heintz.
In April 2009, an FAA "special review team" set out to investigate the failures and to determine if they arose from a common cause. The situation was complicated by the fact that so many versions of the basic design existed and that amateur-built examples could differ in random ways from factory products. The report, issued in January 2010, concluded that, while no single clear-cut explanation of the wing failures could be found, the design was deficient in a number of respects that, taken together, might account for them.
The FAA's critique focused on four areas: wing structure, aileron balance (or lack of it), airspeed calibration and control forces.
With regard to control forces, very small, light airplanes like the 601 are often said to be "fingertip airplanes," and this is praise, not criticism. Low control forces in pitch are potentially a cause for concern, however, because they might allow a pilot to overstress the airplane by a sudden stick movement. The FAA conceded that the 601's pitch force "gradient" — the rate of change of stick force with speed or G-loading — was well-behaved but added, somewhat tentatively, that "flight test data from foreign authorities indicate at aft center of gravity conditions the stick forces do become light." None of the witness accounts mentioned a sudden pull-up, however, and so the low stick forces, while worthy of mention, are not unique to the 601 and do not necessarily rise to the level of a design flaw. The FAA did suggest, however, that the American Society for Testing and Materials (ASTM) "consensus standard" under which the 601 was certified as an LSA ought to specify minimum stick forces for limit G-loads, as federal airworthiness standards do.
The matter of airspeed calibration is tied to the maneuvering and never-exceed speeds, and they in turn affect the pilot's ability to manage G-loads. The FAA observed that "AMD and Zenith Aircraft calibration procedures do not clearly explain how to adequately account for basic pressure source position error due to the location of the pitot-static ports" and calculated that "a 1 mph error in airspeed provides approximately a 0.1 G-load change on the wing at maneuver speed." Cumulative errors in airspeed calibration and in defining VA could result in exceeding allowable gust loadings by nearly 1 G. The airspeed calibration curve supplied by the Czech manufacturer CZAW differed from other curves and suggested very large errors — as much as 24 knots — and the potential for a 2.8 G excess load at the maneuver speed. Again, however, there was nothing in the accident reports to suggest a consistent linkage with vigorous maneuvering or extremely turbulent weather.
Aileron balance was a more serious issue. NTSB investigators had concluded that flutter had occurred in several of the accidents, because damaged components showed that wings had been heavily stressed both upward and downward; overstress due to pilot action usually goes in only one direction. The investigation could not determine whether flutter had been caused by the ailerons, however, or whether some prior structural deformation had predisposed the wing to flutter. It was noted with alarm that deflecting the ailerons to their stops caused visible flexing of wing skins in the vicinity of the aileron bellcrank. Several observers also noted that wing skins would wrinkle under twisting loads applied by a mere human, suggesting, again, an ominous lack of stiffness. The FAA noted that the 601 had never been subjected to a thorough flutter analysis — a complex and expensive procedure — but that there was no point in doing one before wing modifications had been accomplished.
Those wing modifications were required because the FAA found that the stress analysis of the wing had been faulty in several respects. To begin with, the assumed spanwise distribution of lift, which determines the maximum loads experienced by the spar, was unrealistic and "nonconservative" — that is, it made the wing weaker, not stronger. Errors had also been made in allowances for fuel loads, in defining the aerodynamic properties of the airfoil, in interpreting the meaning of ASTM requirements for combined bending and twisting loads, and in setting the maneuvering speed, VA, which was 8 knots higher than it should have been.
Although the manufacturer disputed some FAA findings while accepting others, the wing was modified and subjected to a static test at what the report calls the "ultimate test load." It is not clear whether this expression means the ultimate load, which is 150 percent of the limit load and would be 6 G in the case of the 601, or merely the greatest loading applied in the test; in any case, it was about 5 percent short of what the FAA thought it should be. Some permanent deformation was observed, but that would be expected at ultimate load; the FAA seemed more or less satisfied. It should be recognized, however, that while wing stiffness might play a role in flutter, and flutter, in turn, might play a role in the eventual bending failure of the wing, there is no reason to think that if flutter occurred, the wing would not break even if it were designed to the FAA's standards.
The FAA report, which is written in a colloquial style and is accessible even for lay readers, may be found online at faa.gov. What is interesting about it, apart from the details about one particular aircraft, is the general sense one gets that airplane design, at least at the LSA level, is not an exact science. Graphs of design wing loadings, in particular, display shockingly large disparities between the manufacturer's assumptions and the feds'. Since the 601 is the work of a reputable designer and is produced by well-established firms, one has to suspect that if the FAA conducted an industrywide investigation of LSAs and homebuilts it would turn up a whole lot more of the same kinds of discrepancies.
This article is based on the NTSB's reports of the accidents and is intended to bring the issues raised to our readers' attention. It is not intended to judge or to reach any definitive conclusions about the ability or capacity of any person, living or dead, or any aircraft or accessory.


Sign-up for newsletters & special offers!
Get the latest FLYING stories & special offers delivered directly to your inbox