We Fly: Pilatus PC-24
This sleek jet is actually Swiss, but it seems more Canadian, as if Paul Bunyan has gone Wall Street.
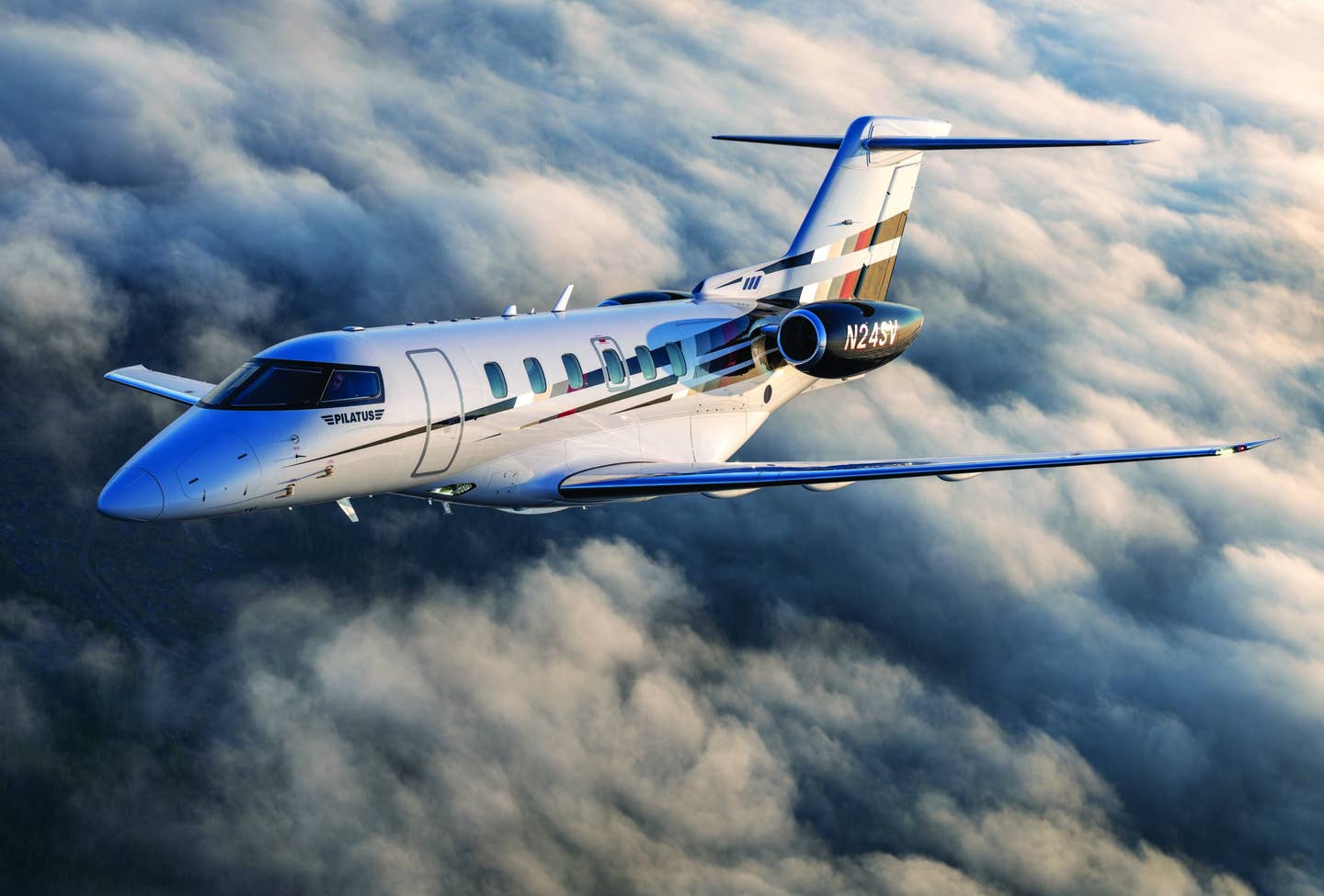
The Pilatus PC-24 in flight. [Courtesy: Pilatus Aircraft]
The jet is Swiss, yet after flying it over three days in wildly varying weather, traffic, and runway conditions, we came away feeling that the appropriate analogy is Canadian. It’s as if Paul Bunyan became a Savile Row suit-wearing investment banker—a regular at the most sophisticated business functions and social affairs, yet would periodically don a red-checked wool shirt, blue jeans and boots, tuck Babe the Blue Ox under his arm and head for the backwoods.
The Pilatus PC-24 is a sleek, luxurious, large-cabin, large cargo area, single-pilot, light jet that is capable of CAT II ILS approaches. It fits smoothly into the highest volume airports, navigating the most complex arrival and departure procedures using cutting-edge avionics and yet, it can use runways as short as 4,000 feet and do what virtually no other jet can do—operate from unimproved runways of grass, gravel, snow, or dirt.
If you're not already a subscriber, what are you waiting for? Subscribe today to get the issue as soon as it is released in either Print or Digital formats.
Subscribe NowSomehow, we weren’t surprised to discover the unique capabilities of PC-24. Its genealogy reveals a company established in 1939 in Stans, Switzerland, near Mount Pilatus that started life doing maintenance and overhauls on established, production aircraft. Within three years it had designed and built the P-2, a two-seat, piston-powered military trainer. The company grew, building subassemblies for large aircraft manufacturers and developing military trainers, both piston and turboprop, as well as the piston-powered PC-6 Porter, which is capable of stunning STOL performance.
Within a few years, the Porter would be powered by a turboprop engine, making it one of the most in-demand STOL airplanes throughout the world, although its cruise speed tended to be measured with a calendar.
By the 1990s, Pilatus had delivered over 1,000 airplanes, most of them military turboprops, then the company turned its attention to creating a utility single-engine turboprop for military and civilian use. Teaming with the Royal Flying Doctor Service (RFDS) of Australia, it made an airplane that was fast enough for ambulance, military, and personal transportation, but rugged enough to go into backcountry airstrips for medical evacuation. It included a gigantic rear cargo door and pressurized cargo area that was connected to the main cabin and an interior that could be rapidly changed from luxury seating to all cargo, or medical transport or “combi”—part cargo, part passenger seating.
The PC-12 proved to fit a niche that few thought existed—essentially a fast, pressurized, Cessna 208 Caravan. It’s now hard to find a place on the planet where one of the more than 2,000 PC-12s in service isn’t in use. Not surprisingly, Pilatus responded to the demand for the PC-12 by setting up a worldwide dealer and parts network and building a sophisticated completion center in on the Rocky Mountain Metropolitan Airport (KBJC) in Broomfield, Colorado, near Denver, as a high proportion of its sales go to U.S. buyers.
Recognizing success when they had it, the folks at Pilatus decided to come up with a swept-wing, single-pilot-capable twinjet that had an even bigger cargo door than the PC-12, capable of cruise speed competitive with other jets in the light jet category, and use short runways, whether paved or not. It became the PC-24—and, no, no one we spoke with at Pilatus was able to explain why its well-known civilian birds had numbers divisible by six. In our opinion, the PC-24 is living up to the nickname given to it by Pilatus—the “Super Versatile Jet.”
The PC-24 has seating for six to eight but can be configured for 10. We consider the cabin space to be more along the lines of a medium jet, than a light one. The pressurized cargo compartment—accessible from outside and the cabin—has a capacity greater than any other light jet—90 cubic feet. With a pilot and six passengers it has an NBAA range of 2,000 nm.
The wing has a variably swept leading edge, straight trailing edge, and an astonishingly smooth upper surface, giving it a high-speed cruise of 440 ktas or Mach 0.74. The sophisticated wing, combined with double Fowler flaps, computer-assisted roll spoilers, and lift dump system allow operations from runways shorter than 4,000 feet. Gross weight takeoff at sea level on a standard day over a 50-foot obstacle is a mere 3,090 feet. Landing, with max flap deflection (33 degrees) over the same obstacle is 2,410 feet.
The Basics
First flight of the PC-24 was in 2015, with FAA certification in December 2017. Certification for rough field operation, including grass, wet ground, dry sand, gravel, and snow-covered surfaces was an involved process that was completed in early 2020.
Power is supplied by a pair of full FADEC Williams FJ44-4A-QPM engines developing 3,420 pounds of thrust each, with 3,600 pounds of thrust in automatic thrust reserve available if one engine fails. TBO is 5,000 hours. Max pressurization differential is 8.8 psi, giving an 8,000-foot cabin at the jet’s 45,000-foot max operating altitude, where it burns 935 pounds of fuel per hour at max-cruise power.
The PC-24 we flew had a basic operating weight of 11,816 pounds (six-seat configuration and one pilot aboard). As it was equipped with nearly every option, it weighed just over 200 pounds more than the number on the Pilatus website. Maximum ramp weight is 18,840 pounds; max takeoff weight is 18,740 pounds. With full fuel, 5,964 pounds (888.5 gallons), 1,060 pounds may be carried in the cabin, or five 200-pound passengers and little baggage. Maximum landing weight is 17,340 pounds, requiring 400 pounds of fuel be burned off following a maximum gross weight takeoff.
Maximum zero fuel weight (sometimes called wing-bending weight—any weight added to the airplane above this number must be fuel) is 14,660 pounds. That gave a maximum cabin load in the jet we flew of 2,844 pounds, a huge load, in our opinion, for a light jet. That left 4,180 pounds of fuel to bring the airplane up to the maximum ramp weight, enough for a three-hour trip with some reserve. We ran some sample weight and balance problems on the jet and noted that the fuel is in front of the center of gravity, but even with the aft CG shift during flight, it was easy to keep the aircraft loaded within the operating envelope.
- READ MORE: We Fly: Tecnam Gran Lusso
We’ll mention here that the ability to carry a load went hand in hand with the large, flat-floored cabin. Its volume is 501 cubic feet, with a height of 5 feet, 1 inch, a width of 5 feet, 7 inches, and length of 23 feet. With the ability to change out seats, install stretchers, make the airplane part people-hauler and part freighter, the Super Versatile Jet title seems most appropriate.
The PC-24 is an electric jet. The only hydraulic system aboard is the brakes. With the sophisticated automation, almost all circuit breakers are virtual or electronic. We counted only eight on the flight deck, near the pilot’s left elbow.
Avionics
We have seen and flown some impressive, integrated avionics packages. In our opinion, the PC-24 meets or exceeds everything we’ve experienced when it comes to supporting a person flying a jet single-pilot.
What Pilatus calls its Advanced Cockpit Environment (ACE) is powered by the Honeywell Apex system—based on its Primus Epic system. It uses a small fleet of computers to manage and integrate all of the systems in the aircraft, including such things as roll spoilers that assist the ailerons at different rates depending on speed and aircraft configuration, the automatic lift dump system that deploys when it senses the correct conditions on landing, automatic fuel balancing, automatic anti- and deicing (hot wings, engine inlets, and pitot heat along with abooted horizontal stabilizer), a utility management system that runs in the background to monitor all valves and sensors and runs trim during flap and air brake deployment, rudder bias to reduce rudder pedal force during engine power imbalance or engine failure, among many more.
The Honeywell avionics system uses four 12-inch displays as its foundation with a PFD in front of each pilot and systems and situational awareness information displayed on two MFDs between the yokes. It includes Honeywell’s SmartView synthetic vision system.
- READ MORE: We Fly: Piper M700 Fury
A cursor control device—a trackball—and buttons are used to control and select everything on the displays except data entry. If a screen is lost, needed information cascades automatically to the remaining screens.
ACE effectively makes using its electronic checklist a requirement, something we found that reduced and focused our workload. Each item on the checklist automatically pulls up the appropriate color-coded system schematic, so you can tell quickly that everything is configured as it should be. In operation, “normal” is characterized as switches up, knobs up, dark annunciator panel, and no aural alerts—a human factors design we appreciate.
The electrical system is powered by two lightweight (36.6 pounds each) lithium-ion batteries. As with the PC-12, battery one is in the nose and battery two is in the tail. The batteries communicate real-time state-of-health and state-of-charge to the ACE. In operation, we were impressed by the lack of drawdown during engine start compared to the nickel-cadmium batteries we’re used to flying, as well as the speed of recovery from the start.
Walking Around It
Not surprisingly, the first thing that grabs one’s attention when approaching the PC-24 is the size of the cargo door. At 51 by 49 inches, it is capable of swallowing bulky loads.
What struck this former freight dog was that there is no sweep to the trailing edge of the wing. That costs the jet some cruise speed, but it means that a forklift or ambulance can approach the cargo area straight on.
After tearing up fingers and hands wrestling pallets and heavy equipment off forklifts that had to approach the cargo door at an angle on Cessna 402s and 404s, we know that there are scores of people in the working world of aviation that appreciate the straight trailing edge design decision. The cargo door itself is retained by six latches and pins. It opens easily by pulling one handle and stepping back as it moves upward. To close, push and hold a button on the right side of the doorway.
Continuing the walkaround, the lower engine nacelles can be rapidly swung open after snapping three latches, making it easy to look over the engine and accessories, and check the oil level. There are no thrust reversers because the low approach speeds and lift dump system make for short landing distances without the extra weight. The top of the nacelles extend aft beyond the engine coverings.
This feature takes advantage of the Coanda effect—the tendency of a slower-moving fluid or airflow to stay attached to a convex surface. It is a sort of mechanical thrust vectoring that helps reduce the nose up control force required on rotation on takeoff and in the flare for landing. In cruise, the airflow is so fast that it breaks up the Coanda effect.
To allow for convenient cargo door access, the engines are mounted farther aft than is conventional. To protect the engine against ingesting foreign object damage (FOD), they are also mounted slightly higher. The major FOD protection is provided by the flaps that deflect debris away from the engine intake.
The nose tire has an unusually wide cross section with a large chine that kicks water and objects away and down. For operation on unpaved runways, a fender is clipped onto the aft portion. This operation takes less than 10 seconds.
Some skull sweat went into the landing gear design. The trailing beam main gear has two tires on each leg, reducing footprint weight for operations on unimproved surfaces—and the tire pressure is a low 70 psi. A white breakaway plastic ring around the top of the hydraulic shock absorber on each gear leg will snap off if the strut reaches full travel during a hard landing giving a clear indication that it has happened.
A similar concept is used on the nose landing gear to indicate potential damage. If a tow turning limit is exceeded while moving the aircraft, a bright green indicator snaps off.
The Cabin
We spent half a day going through the 118,000-square-foot Pilatus completion center and the recently completed 28,445-square-foot paint facility where we saw unpainted, green jets that had been delivered from Switzerland converted to islands of luxury in the sky.
When we walked into the large, quiet room where the seats are built up, our first thought was, “This is where the artists live.” We were right. We watched leather from Europe—where there is no barbed wire to injure cattle—be carefully inspected for scars, bug bites, abrasions, or other imperfections before being placed on a table where a computer and master craftsman teamed up to decide how many pieces of varying shapes could be cut from it based on its size and the quality of each section. The finest portions would be clearly visible to occupants. All scrap leather is given to the local VFW for a program that makes use of what would otherwise be waste.
We saw one seat that had nearly been completed when the technician discovered a subtle imperfection in a section of leather. The technician immediately stopped work. We don’t know how far the seat would have to be disassembled to fix the problem, but it looked like the fix was going to be expensive. That level of attention to detail and determination to make something right is what Pilatus consumers have come to expect.
The seat assembly area set the tone for what we saw throughout the completion center. Pilatus brought the paint process in-house to better control quality. It designed three paint booths with air flow that can be controlled through each part of the process. Lasers are used to guide masking of the paint schemes and Pilatus makes its own paint so that it can be sure that each batch of a color is identical.
Workers took time to answer our questions about various processes. We saw a great deal of pride in their work that was reflected in the finished product.
Opening the airstair door of a completed PC-24—it’s rugged but moves with fingertip effort—gave access to an interior befitting this class of jet. We particularly liked the flat floor and the cabin accents. The pullout tables open to a completely flat surface. The seats move out from the wall, rotate, and most will lay flat. The key takeaway here is that the seats are mechanically operated, not electric, so they can be easily removed to accommodate a cargo conversion fairly quickly and easily.
The headliner has virtually no head knockers. There are plenty of USB ports and a sophisticated in-flight entertainment system and Wi-Fi.
Flying It
We have never had such an easy time getting into the left seat of a jet.
The geometry of the center console and seat helped, but the fact that the yoke came out of the panel rather up from the floor made all the difference. Once in place the seat adjusts to fit almost any pilot physique. The rudders adjust fore and aft via an easily reached crank.
From occupant protection and human factors standpoints we liked what we saw. The restraint system is four point and there is flail space in front of both pilots with nothing to hit up and forward on the headliner. There is an overhead panel, but it is centered over the power levers and not in a position where a pilot will slam into switches in a quick stop. The power levers fall comfortably to hand and the trackball used to navigate the Honeywell avionics is easy to find and hold, something we like in turbulence.
Using the electronic checklist provided by ACE, we tracked system schematics as we clicked through the prestart tasks. We found that ACE was intuitive and presented information needed when it was needed. It appeared to us to be designed to keep the workload for a single pilot manageable.
Starting the Williams engines was a matter of rotating a selector to “run,” holding the start button for two seconds, and then monitoring the start as FADEC managed it. The right engine can be run in Quiet Power Mode (QPM), which drops rpm by 8 percent, reduces the noise level, dropping fuel burn to 140 pounds per hour, and allows it to function as an APU, saving the weight of an APU. The good news for owners is that the time the engine is run in QPM as an APU does not count toward the TBO.
A flight plan can be loaded into the system directly or uploaded from ForeFlight. Once loaded and the pretaxi checklist complete, we headed for Runway 12R at Rocky Mountain Metro. V1 was calculated to be 94 kias, with VR at 97. The plan was to climb to FL 450 and fly to Alamosa to do landings, then do airwork and demonstration of safety features on the way back to Rocky Mountain.
The power levers have detents for maximum continuous power, takeoff power, and automatic thrust reserve. Acceleration is brisk, even at a mile-high airport. Rotation requires a long pull on the yoke to raise the nose, then pitch forces were lighter than we expected and control response in all axes was brisk.
We saw a rate of climb of slightly over 4,000 fpm at a weight well below gross. ATC demands precluded a climb straight to FL 450. However, once there, we saw Mach 0.72 and 411 knots true airspeed on a fuel burn of just under 1,000 pounds per hour.
Pilatus chief pilot Gerard Lambe had us make 45-degree banks in each direction to demonstrate high-altitude handling. It was as if we were maneuvering at below 10,000 feet—there was no buffet.
As we headed south, thunderstorms began popping up. That gave Lambe an opportunity to demonstrate the abilities of the Honeywell RDR 7000 radar system. It automatically does all those things we worked so hard to learn years ago, control tilt to get accurate cross sections of weather and predict attenuation. Put simply, the radar presents weather of interest along your route of flight, vertically and horizontally. If there are thunder boomers out there that aren’t going to affect you due to your route or altitude, they are presented with cross hatches through them, so you can focus on what is important to you. It ranges out to 300 miles and provides predictive hail and turbulence out to 60.
The RDR 7000 made it easy for us to rapidly decide that Alamosa was out of the picture for that day, so we diverted to Pueblo for our landings.
As we descended Lambe described the emergency descent maneuver the PC-24 is programmed to perform should there be a loss of cabin pressure. The aircraft will turn 90 degrees and descend to 15,000 feet, where it will set up cruise at 180 knots. Additionally, the pressurization system is designed to not allow the cabin altitude to get above 14,500 feet, even if the cabin dump is pulled to evacuate smoke. That way the pilot can’t mess up and become incapacitated. If the cabin gets above 14,500 feet, it’s because something blew out.
We made a series of landings at Pueblo at flaps 15 and flaps 33 as well as a coupled single engine missed approach to demonstrate the rudder bias and automatic yaw control. We found the jet to simply be fun to fly in the pattern. There was little pitch change with flap, gear, or speedbrake extension—the automation runs the trim.
With VREF speeds under 100 kias, we observed that it was surprisingly easy to hold the desired speed within a knot or two. We were told that the pitch trim does not run continuously when the dual switches are moved but rather in pulses to prevent the possibility of a trim runway. The pulses were smooth enough and close enough together that we could not detect them.
Lambe advised that the PC-24 will float quite nicely on landing, so extra speed on final is not your friend. Pulling the power to idle at 50 feet, on ref, and flaring gently at 20 feet or so resulted in landings without float. Standing on the brakes once the nose was down gave the lift dump system time to put the weight on the wheels, and we stopped right bloody now—pressed against the shoulder harnesses.
Coming out of Pueblo we leveled at 15,500 feet to demonstrate some of the safety systems of the PC-24. Auto speed protection uses pitch and the autothrottles to prevent overspeed and underspeed with the autopilot on. With the autopilot off, it gives tactile feedback to encourage the pilot to reduce the bank angle or change pitch to avoid an upset or overspeed or underspeed—if the pilot doesn’t act, the feedback becomes more insistent.
Stall protection is provided by a stick shaker and pusher. When the pusher activated amid flashing “Hey, you’re gonna stall!” lights and aural warnings, it lowered the nose smartly, reducing the AOA. We helped it along then brought up the power levers and easily changed a descent into a climb.
On the way back to Rocky Mountain Metro, the RDR 7000 provided us with the information we needed to make the decision to return or divert. It helped us find a route home around the developing cells. We didn’t even get wet until we turned final. The landing gave us a chance to see what the jet could do in adverse conditions. Maximum tailwind on landing for the PC-24 is 10 knots, which is what we had. The grooved runway was wet in moderate rain.
Even with a tailwind, it was no problem to stay on glideslope while following Lambe’s guidance to not add extra speed on final. Once on the ground, we lowered the nose and Lambe asked us for maximum braking to see how well the jet tracked on a wet runway. Once again, it felt as if someone had tossed out an anchor. Using the rudders assertively allowed the jet to track where we desired and come to a stop in a hurry.
Backcountry
Two days later, we installed the nosewheel fender and figuratively donned blue jeans, lumberjack shirts and boots, and loaded Babe the Blue Ox in the cargo area—well, no, actually it was a lot of photography gear.
We arrived shortly after sunrise for a flight demonstration of the aircraft’s landing capability on unimproved runways at the Smiley Creek, Idaho, backcountry strip. At an elevation of 7,206 feet, the grass runway is 4,900 feet long, sloping upward to the south, with landings generally to the south and takeoffs north. We were joined by a Pilatus PC-12 and turboprop PC-6 as well as several Cessnas, Cubs, and Huskies that had flown in for breakfast at the popular lodge.
We have been flying off grass strips in piston-powered airplanes for over 50 years and have had some adventures on wet grass on landing and long grass on takeoff. We enjoy operating from grass but were wondering how it would be in a jet and whether the antiskid system would stop us in a reasonable distance.
Bottom line: No problem. Lambe did three takeoffs and landings and, from the right seat, I couldn’t tell the difference between pavement and grass. On the first landing, Lambe got on the brakes hard, and the airplane slowed to a walk after using maybe half of the runway. I was concerned that we had rutted the runway because our deceleration was so rapid. We parked and I had a chance to look at the runway—no ruts. The relatively low-pressure tires and dual main gear meant the footprint weight didn’t tear anything up.
On the second takeoff the wind had started to blow from the south, but we took off to the north as is the local practice. We used slightly less than two-thirds of the runway by our eyeball estimate. We then landed to the south for a third time, stopped, discussed our takeoff plan, and loaded up photographers and gear. The wind had picked up, so we decided to take off into the wind and uphill.
It was no big deal. We rolled about the same distance as we had on the previous downwind, downhill takeoff and blasted away from the rising ground ahead of us. It was a hoot.
Conclusion
At a base price of about $9.5 million and $13,614,400 equipped in the airplane we flew, the PC-24 represents a very attractive flying machine. It will do what all light jets will do with ease, albeit slightly slower because of its larger cabin cross section. Then it will do things some won’t do, such as shoot CAT II ILS approaches with two pilots aboard.
And the PC-24 will do something that none of them can do—operate from unimproved strips to take advantage of thousands of other locations worldwide that just might be closer to where you need to be to do the business or have fun off the beaten path.
Cockpit at a Glance: Pilatus PC-24
A. The Honeywell Advanced Cockpit Environment (ACE) uses four 12-inch displays as its foundation with a PFD in front of each pilot.
B. A trackball is used as a cursor control device to select almost everything on the displays. It is retained in a structure that facilitates easy inputs even in turbulence.
C. The two 12-inch ACE displays mounted in the center of the panel are for systems monitoring and situational awareness information.
D. The control yokes extend from the panel rather than a floor-mounted pedestal, making it easier to get into and out of the pilot seats than in other comparable jets.
Spec Sheet: Pilatus PC-24
Price as Tested: $13,614,400
Engine: Two Williams FJ44-4A-QPM
Engine Thrust: 3,420 lbf. per engine; 3,600 lbf. automatic thrust reserve
Length: 55 ft. 2 in.
Height: 17 ft. 4 in.
Wingspan: 55 ft. 9 in.
Wing Area: 332.7 sq. ft.
Wing Loading: 56.3 lbs./sq. ft.
Power Loading: 2.74 lbf./sq. ft.
Cabin Width: 5 ft. 7 in.
Cabin Height: 5 ft. 1 in. (continuous flat floor)
Max Takeoff Weight: 18,740 lbs.
Max Zero Fuel Weight: 14,660 lbs.
Basic Operating Weight: 11,559 lbs. (executive six-seat configuration, including one pilot)
Max Payload: 3,100 lbs.
Useful Load: 7,281 lbs.
Max Usable Fuel: 5,964 lbs. (888.5 gallons)
Service Ceiling: 45,000 ft.
Max Rate of Climb, MTOW, ISA, SL: 3,960 fpm
Max Cruise Speed: 440 ktas
Max Range: 2,000 nm (NBAA IFR reserves, single pilot, six passengers)
Fuel Consumption at Max Cruise: 935 lbs./hr. (FL 450, ISA)
Stall Speed, Flaps Up: 106 kias
Stall Speed, Full Flaps: 83 kias
Takeoff Over 50 Ft. Obs: 3,090 ft. (ISA, sea level @ MTOW)
Landing Over 50 Ft. Obs: 2,410 ft. (ISA, sea level @ MTOW)
This feature first appeared in the October Issue 951 of the FLYING print edition.


Sign-up for newsletters & special offers!
Get the latest FLYING stories & special offers delivered directly to your inbox