World’s Largest Airplane Flies a Fourth Time for Mission-Critical Test
Stratolaunch’s Roc, the world’s largest airplane, made its fourth test flight Thursday over California’s Mojave Air and Space Port with a mission of fully operating all landing gear in flight for the first time.
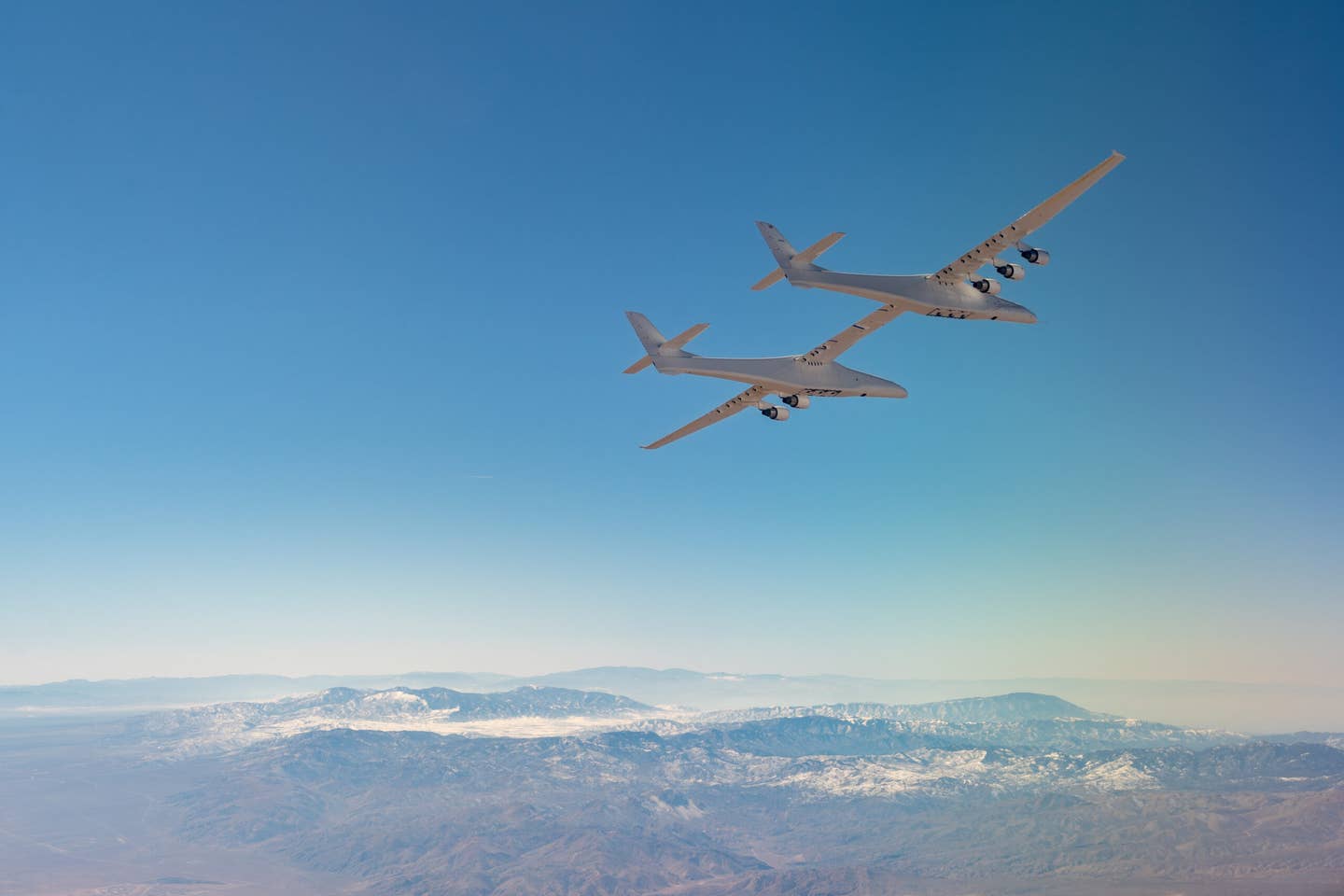
The largest airplane in the world by wingspan flew its fourth test flight, successfully cycling through all landing gear for the first time. [Courtesy: Stratolaunch]
Stratolaunch’s Roc, the world’s largest airplane by wingspan, successfully completed its fourth test flight Thursday, on a critical mission aimed at cycling through all landing gear for the first time.
Taking off at about 12:23 p.m PT from its base at California’s Mojave Air and Space Port (KMHV), Roc reached a maximum altitude of 15,000 feet and spent an hour and 43 minutes in the air, lifted by its gargantuan 385-foot wings.
Time to stretch those legs! We just successfully retracted and extended our full landing gear for the first time. #LetsRoc pic.twitter.com/UUVhC1xmy0
— Stratolaunch (@Stratolaunch) February 24, 2022
With a Cessna 550 Citation Bravo chase plane flying nearby, it wasn’t long before the six-engined, twin-fuselage Roc successfully retracted all eight gear, showing a much sleeker profile against a clear blue sky. A few minutes later, the gear reappeared, fully extended.
Demonstrating successful retraction and extension of all landing gear was mission critical for Roc and the most important part of this fourth flight test. Verifying full gear operations is a requirement before Roc can move forward in its flight test campaign and eventually serve as a carrier platform to launch hypersonic testbed vehicles.
“Today’s successful flight demonstrates and validates improvements to the carrier aircraft’s systems and overall flight performance,” said a statement by Dr. Zachary Krevor, Stratolaunch president and COO. "The full landing gear retraction and extension brings the carrier aircraft closer to operational status, a milestone that is necessary to ready the aircraft for Talon-A separation and hypersonic flight test later this year.”
The Gear
Quickly, let’s break down the landing gear:
- 6 main gear, each with four-wheel bogies
- 2 nose gear, each with two-wheel bogies
- Total gear: 8
- Total wheels: 28
- Total number of brakes: 24
- Total number of moving panels that comprise the landing gear door system: 34
- Roc’s gear and various other components were acquired from existing Boeing 747-400 airliners.
Roc also includes original systems and components as well as components from Cessna, Gulfstream, and other OEMs.
Demonstrating that Roc can retract and extend each of its six main gear and two nose gear in the air, per design standards, required precise coordination and communication between flight crew and Roc’s control room on the ground. Verifying full gear operations was required before Roc could move forward in its flight test campaign and eventually air-launch hypersonic testbed vehicles.
The Control Room
In the control room during the flight was Stratolaunch lead systems engineer Stuart Yun, who told FLYING earlier this week that, perhaps surprisingly, the Boeing gear hasn’t been modified to accommodate stresses and pressures created by Roc’s unique twin fuselage.
“We haven’t modified the gear in any way, but we have modified the systems and how they interact with our airframe,” Yun said. “The original design is incredibly robust.”
During Roc’s flight last month, in what you might call a test before the test, the aircraft successfully retracted and extended the left fuselage’s middle main gear alone. This was a precautionary measure to ensure the airplane would be able to land if something had gone awry. Aside from a bit of minor vibration on the gear doors, all went as planned.
"30 Seconds of Fear"
Inside the control room, Yun and his fellow team members were tasked with monitoring the gear during all phases of the flight, using screens placed across multiple workstations. Each team member indicates the time is right and verifies all systems are working properly. Then the flight test conductor—or TC—relays that information, and if necessary, any abnormalities that may be occurring, to the flight crew aboard Roc.
Then, the flight crew goes ahead and puts Roc’s gear handle in the up position.
It is at this point, Yun jokes, when “there’s about 30 seconds of fear.” Everyone in the control room has their eyes on their screens, Yun says, checking the sequencing and indicators to confirm the gear were retracted and extended successfully.
To verify the gear has retracted properly, the team uses an array of sensors, including on-board cameras, extra hydraulic pressure transducers, and extra limit switches.
With all gear retracted, engineers were able to gather real-world data about Roc’s performance and flight handling characteristics. These numbers will help the aircraft’s developers form more accurate expectations for operational missions. Those missions, which are expected to begin next year, will launch hypersonic testbed vehicles for U.S. government and commercial research.
Finding Workarounds
Integrating the Boeing landing gear with Roc hasn’t exactly been easy. Some of the most challenging parts of the job have involved using systems within the gear that weren’t necessarily designed to operate the way Roc’s engineers wanted. However, during the build, engineers had the benefit of accessing the Boeing fleet database that was used to maintain the 747-400 gear. This opened the door to repair type manuals, often referred to as a CMM (component maintenance manuals). Engineers were able to refer to these manuals for details such as how to rebuild an actuator or how to rig nose gear.
Some situations required finding workarounds.
In fact, some of the systems on the gear had to be reverse engineered to fully learn how they functioned before the gear could be integrated into the airplane.
For example, to model landing gear loads, engineers had to take apart a Boeing gear to determine all the internal dimensions and flow characteristics of the hydraulic dampers. They also performed significant testing on components to determine how they work.
These Are the Brakes
With the landing gear, of course comes Roc’s braking system—also designed and built by Boeing and originally intended to stop a 747-400, which has an empty weight of about 403,000 pounds.
“We have 24 carbon brakes, so we have quite a bit of stopping power,” Yun said. “Each one is capable of absorbing an incredible amount of energy. These brakes can be tricky to work with at times but they provide the performance we need for an aircraft this size.”
Braking starts when the feet of the pilot in control hit the brake pedals, activating a cable system connected to a brake metering valve, which supplies a specific amount of hydraulic pressure to the brake stack. That way the pilots have the ability to modulate how much clamping force is applied to each side of the aircraft.
What kind of force? Enough to bring Roc—with an empty weight of half a million pounds—to a complete stop.
Surprising Flight Characteristics
As you might expect, flying Roc is challenging. In fact, pilots have told FLYING that the aircraft has demonstrated a few surprising flight characteristics during its previous test missions. In addition, piloting Roc while sitting in the right fuselage makes lining up for final approach a little tricky. You’re not looking straight down the runway’s center line, which makes the maneuver a bit like landing an airplane mounted on a gigantic pair of in-line skates.
Extra Wide Load
Roc is the world’s largest airplane by wingspan, measuring longer than any airplane in aviation history, including the Airbus A380, Boeing’s 777-9, Howard Hughes’ H-4 Hercules (The Spruce Goose), and Antonov’s An-225 Mriya.
In fact, Yun said the maximum gross weight of the Antonov An-225 is very close to Roc’s designed maximum gross weight of 1.3 million pounds. “Just to put that in perspective, we designed this thing from the get-go to handle 1.3 million pounds,” Yun said. “Hopefully, we’ll get there someday.”
Last month’s mission was the most productive so far for the one-of-a-kind jet. During the four-hour and 23-minute flight, Roc successfully expanded its test envelope by:
- reaching a maximum altitude of 23,500 feet
- achieving a top speed of 180 kias
- successfully retracting and extending the left middle main landing gear
- flying two low-approach maneuvers over the runway before landing
In addition to its third flight last January, Roc’s previous test flights took place in April 2021 and April 2019.
What's Next for Roc
Now that Roc has completed its fourth flight, engineers plan to install a pylon under its center wing, which will enable it to carry smaller aircraft and other heavy payloads. The center wing measures 95 feet between fuselages and is designed to support up to 500,000 pounds. Gathering data on how the pylon affects Roc’s flight dynamics will be part of the airplane’s fifth test flight.
Roc was first conceived as an inflight launch platform for low-orbiting satellites. Eventually, its main mission shifted toward air launching hypersonic testbed vehicles. For that reason, Stratolaunch is developing Talon—a series of uncrewed, autonomous, rocket-powered aircraft designed to fly at Mach 5 or faster.
The Pentagon’s Missile Defense Agency has contracted with Stratolaunch to provide “threat replication” data to help scientists understand how to engage and intercept hypersonic threats. If Talon development and Roc’s test flights remain on track, the company expects to conduct Talon’s first hypersonic test flight by the end of this year.
A little background info for those who haven’t been following Roc: Created in 2011, Stratolaunch was the brainchild of the late Microsoft (NASDAQ:MSFT) co-founder Paul Allen. Roc—also known as Model 351 Stratolaunch—was built by Scaled Composites, the iconic company founded by legendary aerospace engineer Burt Rutan. In the wake of Allen’s tragic death in 2018, Stratolaunch’s parent company, Vulcan, sold it to the U.S. private equity firm Cerberus Capital Management.


Sign-up for newsletters & special offers!
Get the latest FLYING stories & special offers delivered directly to your inbox